How to meet demand for electricity in mining
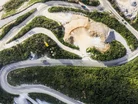
Electrifying mining may be an ambition for many companies looking to reduce their carbon footprints and energy costs, but reaching that goal will also mean significant investment.
That’s according to a new report from McKinsey that says electrifying mines could double the demand for electricity. This will require some serious investment in the power infrastructure, with McKinsey saying this could top US$45 billion for the iron ore industry alone.
However, the potential benefits are just as eye-catching. Energy costs could be reduced by up to 70%, while the all-important carbon footprint could be reduced by as much as 80%.
Of course, this is not some unachievable target, as the report authors – Marc Henrio, Otto van der Ende, Gabriel Motta, and Raj Kumar Ray – tell Mining Digital.
“There are already 100% electric underground mines around, and it is definitely a possibility that fully electric open pit mines should start to come up in the future as the equipment technology matures.”
While companies such as Epiroc are already producing battery electric vehicles (BEVs) suitable for underground use, the sheer scale of open pit mining machinery means the technology needs to advance to make it commercially viable.
Mining has a critical role to play in the transition to a net-zero economy and mining companies are under increased pressure from consumers and investors to clean up their act. It is therefore vital to secure access to significant amounts of renewable electricity to turn mines fully electric and replace diesel.
McKinsey says electrifying the global iron ore industry would require as much as 11 gigawatt-hours of additional electricity per metric ton of iron ore.
The consultancy says that once electric haul trucks become available, the need for electricity could double, simply by replacing 27 diesel trucks and the associated equipment.
So where could this extra electricity come from?
“The best solution to supply electricity to remote operations depends largely on the geographical context of the mine,” says McKinsey.
“Some remote regions have significant solar/wind potential, and those solutions tend to be the cheapest option in high potential areas. In the future, as storage alternatives get more competitive (battery storage, long-duration energy storage), the grid stability issues related to solar/wind could reduce, making it more feasible to run whole operations based on those energy sources.
“When solar and wind potential is not high, small modular reactors (SMRs) could be an alternative to be evaluated, together with carbon capture and storage (CCS) for abating emissions from fossil sources.”
Generating the electricity is one challenge, storing it is another. As the experts from McKinsey say, developments in battery technology will help smooth out those demand curves.
One company already leading the charge on battery tech is Skeleton Technologies which has developed what it calls the ‘SuperBattery’. This graphene-based battery is being developed to power dump trucks for a Shell-led consortium for electrified mining.
These dump trucks could be fully charged with 400kW of electricity in just 90 seconds – 100-times faster than standard lithium-ion batteries. The SuperBattery also has an extended lifespan, lasting for around 50,000 cycles compared to 4,000 for lithium-ion.
The key challenges of electric mining
Electrifying mines is challenging but has the potential to generate considerable value. Here are the key challenges:
Large capital expenditures requirements. The costs for implementing the power infrastructure for electrifying the iron ore industry alone could reach US$45 billion. This will surely mean that new sources of capital (such as green bonds) will be needed.
Large infrastructure improvements. Mines will need to upgrade grid connections, build on-site networks, and install or contract renewable-power capacity.
BEV technological challenges. Battery technologies need to achieve higher density, lower costs, faster charging rates, and larger scale to make electric equipment competitive.
McKinsey says that adapting the operations to a new type of technology presents multiple challenges, and has the following recommendations for a successful transition to electric.
Before the actual implementation of electric equipment:
- Adapt the mine planning and the operations planning to the new equipment – eg. location of charging stations, design of ramps and haulage ways
- Funding the investment for equipment and infrastructure
- Build the infrastructure at site (access to electricity, transmission, charging)
- Obtain access to the equipment, in a scenario where most companies are competing for a limited supply of electric mining equipment
When implementing and operating electric equipment:
- Upskill the operators and maintainers to adapt to the new type of equipment
- Adapt the operational strategy (eg. dispatch logic with energy management, rotation of crew during charging downtime)
- Adapt the maintenance strategy (eg. inventory of parts, batteries, maintenance of chargers, power infrastructure)
While those challenges may seem a barrier right now, the potential gains mean the effort (and expense) will be worthwhile. Those opportunities are:
Operational expenditure. Electrification could reduce energy costs by as much as 70% and reduce maintenance costs for mobile equipment by around 30%.
Operational improvements. Electric equipment could allow for steeper ramp designs, lower stripping ratios, faster cycle times, and less-frequent breakdowns.
CO2 emissions reduction. A fully electrified mine with renewable power could have a carbon footprint that is 80% lower. As well as being good for the environment, this could also avoid carbon taxes and capture potential green-product premiums.
As well as those benefits, McKinsey points to improved working conditions, especially in underground mines (for instance less noise, vibration, better air quality).
In the longer term, mine operators could redesign the mine, adapting to hauling in declines, steeper ramps potentially leading to lower stripping ratios. There would also be lower infrastructure requirements for ventilation in underground mines.