Weir wins $125mn machinery order for Fortescue Metals iron ore project
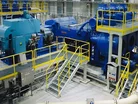
The Weir Group will manufacture a range of Weir crushing and pump equipment to meet a $125mn order from Fortescue Metals for its magnetite iron ore project in the Pilbara, WA.
The Iron Bridge Magnetite Project is a joint venture between Fortescue subsidiary Magnetite Pty Ltd and Formosa Steel located 145km south of Port Hedland. The £100mn ($125mn) order features Enduron High Pressure Grinding Rolls (HPGRS) and GEHO pumps, which will reduce energy consumption and wet tailings waste by more than 30% compared to traditional mining technologies.
The Iron Bridge project is a $2.6bn investment in premium magnetite iron ore reserves with annual production, when the mine is fully operational, of 22 million wet metric tonnes per annum. Delivery of the first ore is expected in 2022.
Weir’s CEO, Jon Stanton commented: “We are delighted to have secured this landmark contract, which is Weir’s largest-ever individual mining order. Fortescue challenged us to help create one of the most energy and cost-efficient magnetite ore processing facilities in the world.
Our engineers have worked relentlessly to design a solution that is truly innovative – delivering significant energy, water and cost savings. This is a great example of working in close partnership with an ambitious customer who shares our passion for using innovative engineering to make mining more productive and sustainable.”
SEE ALSO:
Fortescue Metals Group breaks ground on $1.275bn Eliwana mine and rail project, Pilbara
Fortescue autonomous Caterpillar truck program gears up at Cloudbreak
Fortescue Metals Group approves $2.6bn Iron Bridge expansion at Pilbara
Read the latest issue of Mining Global here
Weir’s Enduron HPGRsare increasingly replacing conventional mills in comminution (crushing, screening and grinding) circuits because of their substantially lower energy consumption and potential for significant total cost of ownership reduction.
Not only do they require as much as 40% less energy than traditional alternatives, but their wearable components last much longer and the maintenance time required to replace worn out parts is significantly lower.