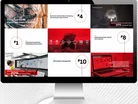
Which are the digital applications with the best value and user acceptance for the mining industry, based on ABB's experience on the ground? Click through to find out.
10: Information management
Information management enables real time visibility and optimisation across multiple sites. It can help with scenario based planning, and help focus on production and environmental targets.
09: Asset management and condition monitoring
Asset management can save millions in costs by eliminating needless maintenance, predicting faults before DCS alarms, and providing recommendations for more proactive plant asset management strategies.
08: Advance process control and analytics
Advances process control and analytics can increase mineral recovery by 1-2% while reducing consumables. Manual controls can be replaced by smart automatic process adjustments, which can sustain production at the optimum level.
07: Integrating process and power control
Integrating process and power control can simplify troubleshooting, increase safety and save 20% on training costs. Operators can be less burdened and centrally supervise larger areas and speed up remote troubleshooting.
06: Predictive maintenance for grinding
Predictive maintenance for grinding avoids mill down time, and saves at least 100 hours per year. Operations managers can predict critical situations, prevent damage to expensive gearless mill drive equipment and avoid costly downtime.
05: Remote monitoring of conveyor belt fleet
Remote monitoring reduces the need for manual intervention in risk areas. It helps catch misalignment or speed issues online, and avoid falling material, energy waste, excessive belt wear, rupture or fire.
04: Material flow monitoring and stockyard optimisation
Material flow monitoring can increase stockyard productivity between 5-10%, providing contracted materials much faster and more reliably.
03: Remote hoist monitoring
Remote hoist monitoring helps optimise production capacity, enabling operations managers to be notified about performance issues, and quickly get the hoist back on maximum capacity.
02: Ventilation on demand
Ventilation on demand improves safety and saves up to 50% energy per year, creating healthy working conditions in the mine 24/7, and enabling energy saving targets to be reached thanks to AI-assisted optimisation models.
01: Automated production scheduling and execution
Automated production scheduling increases productivity by 5-10% and enables mine planners to react to disturbances in seconds using software to automatically reschedule interconnected tasks, minimise delays and idle times.