Industry 4.0 Technologies Revolutionise Mining Operations
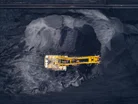
The mining industry is witnessing huge transformation as it embraces Industry 4.0 technologies, which are reshaping operations, improving safety, and enhancing productivity across the sector.
Industry 4.0 is the integration of digital technologies into industrial processes. In the context of mining, this includes the use of Internet of Things (IoT) devices, advanced sensors, and data analytics to optimise operations.
The IoT tends to be consumer-facing, typically involving wearable devices and smart home technology. A subset of IoT is Industrial IoT (IIoT). This consists of internet-connected machinery and advanced analytics platforms that process the data generated by IoT devices, which range from tiny environmental sensors to complex industrial robots.
IIoT technology is revolutionising a range of industries, including agriculture, healthcare, financial services retail and even advertising.
Mining, too, is adopting the technology, and companies such as Madison Technologies – a specialist in scaling network infrastructures – exist to bridge the gap between the technology providers and mining operators.
In a paper for Mining Journal about IIoT in mining, Tawanda Zvarivadza – a Mining & Rock Engineer at Luleå University of Technology in Swede – says: “Given the advantages that IoT brings to the forefront, it makes sense that so many mining companies have raised their investment following the implementation of IoT-enabled solutions in their organisations.”
Paul Collabro is CEO of Madison Technologies, and explains the significance of IoT in mining: "IoT allows mining companies to gather real-time data from various points of operation, enabling informed decision-making and predictive maintenance.”
A major advantage of IoT in the mining industry is its ability to monitor remote and potentially hazardous operations without human intervention, a use case Collabro illustrates with an example.
“By deploying IoT sensors along rail lines, mining companies can continuously monitor critical parameters such as temperature,” he says. “This data can then be used to make crucial operational decisions. Operators can either slow down the rail carts, or see if there's an alternative path."
Another major application of Industry 4.0 technologies in mining is the use of advanced camera systems. These are not just for surveillance but increasingly are being used as sensors to monitor various aspects of mining operations.
Collabro shares an example: "We have a client who approached us about a situation on a mine site where there was a fatality on site involving a truck, because of a blind spot."
In response, Madison Technologies developed a solution using cameras as sensors. Collabro explains: "We came up with a solution that gave them eight cameras on the outside of this loading truck that fed images back to the control room, so they could detect objects – whether this was a person or another asset. By providing drivers with a comprehensive view of their surroundings, potential accidents can be prevented.”
As mining companies continue to adopt Industry 4.0 technologies, the focus increasingly is on how to use the vast amounts of data generated. IIoT technology is improving safety and productivity in mining but works best when there is stringent data discipline.
Of this, Collabro says: "As we see it the challenge with IoT is the amount of data points it will collect. Often all you need is just one piece of insight from all those data points in order to make the decision or make a calculation, yet it's grabbing so much information."
Another technologist extremely well placed to offer insight here is Andy Hancock, who is Global VP, Centre of Excellence, SAP Digital Supply Chain. The Centre of Excellence is like a global SWAT team of industry experts, serving SAP colleagues in the field, with knowledge transfer.
Hancock points out that IIoT networks generate mountains of data and warns that powerful 5G technology – with its huge data capabilities – can “make people lazy, and so they end up throwing tons of information around just because they can”.
He adds: “The trouble is that when you scale-up this approach to enterprise level you soon end up with 50 million data points that flood the network, making it inefficient.
Hancock adds that a danger is that businesses who fall into this trap then end up “chucking more technology at the problem”, where really what they should be doing is “coming back to fundamentals”.
Hancock says the secret to working with big data, like that generated by IIot networks, is “to always be looking out for exceptions”.
He adds: “Think of a temperature gauge on a piece of equipment that is feeding back data. As long as everything is running okay, the equipment will always be roughly the same temperature.
“You don’t need to keep feeding back data about that piece of equipment. The only data you want to capture is if something changes – for example, if the thermostat fails.”
Hancock adds: “IIoT devices are creating data 24/7, so the idea is to discard most of it and look for the exception - the piece of data that shows a machine is overheating, or out of calibration. With data, less is usually more.”
He urges businesses who are harnessing IIoT tech to treat their networks in the same way the world treated modems, back when the Internet was in its infancy.
“Think back to the days of dial-up modems,” he says, “where everyone minimised the amount of data transmitted, because if you didn’t then the whole thing just hung”.
As well as focusing in on data exceptions, Hancock says IIoT operations benefit hugely from edge computing, which is a distributed computing model that brings computation closer to the sources of data – a mining operation, say, or an ore-processing plant.
“If you have local processing power it can be invaluable,” Hancock says. “For instance, if a machine is going out of tolerance and there is a delay in sending this data to the cloud and back, you could have big problems by the time the machine is switched off.
“The idea is that local machine-learning tech understands that a machine is out of tolerance, and recalibrates it without any human action needed.”
To read the full story in the magazine click HERE
Make sure you check out the latest edition of Mining Digital and also sign up to our global conference series - Manufacturing LIVE 2024
Mining Digital is a BizClik brand