Recovering critical materials to save the planet
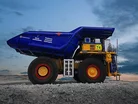
Every day, vast volumes of critical resources, precious metals, minerals and chemicals, are thrown away. Inefficient waste management, consumer behaviour and a lack of awareness means that some of these materials only have a single-use life, when they could be recovered and their value put back into the economy.
The World Economic Forum estimates that just 20 per cent of global e-waste is recycled, while the other 80 per cent ends up in landfill or is incinerated. Among this waste is a significant amount of ‘critical materials’ – including high value metals like gold, silver, platinum and lithium that are widely used in PCs, laptops, mobile phones and batteries. But not everything is thrown away. Many of us have older devices, which incidentally usually have larger amounts of precious metals in them, languishing in kitchen drawers or in under stairs cupboards as a ‘just in case’ back-up or waiting to be dealt with. The so-called ‘urban mines’ in homes across the UK can contain around 50 times the concentration of critical metals than original sources – and are far less hazardous to harvest, if you know how.
The UK government has recognised the value of urban mining and in July 2022 launched a Policy Paper, Resilience for the future: The UK’s critical minerals strategy. It calls for us to make better use of what we have by accelerating the recovery, recycling and reuse of critical minerals and components to alleviate pressure on primary sources in the ground.
Ironically, an unintended consequence of the Net Zero drive towards a safer, sustainable planet is an increase in demand for critical materials like lithium, nickel, cobalt, manganese and graphite. These are essential for the batteries and permanent magnets used in wind turbines and electric vehicles.
Relying on primary sources to extract the volume of materials we are going to need to achieve the energy transition is problematic for many reasons. Critical materials are typically mined from a small number of countries or sites. The current energy crisis has shown us that it is unwise to rely heavily on resources from a single supplier – whether for gas or gold. Some of the regions where materials are mined are politically unstable, often because of the high value of the materials concerned, leading to the idea of ‘war minerals’.
Then there is the cost. Critical minerals are expensive to extract from primary sources and may come with a high human or ethical price tag. What’s more, they involve processing large volumes of extraneous ore to achieve relatively small amount of the required materials, compared to the concentration of materials in devices that are no longer in use.
While there is a great deal of critical material in circulation that is embedded in equipment and products that are reaching the end of their initial use, the materials themselves still have a lot of life in them, and their disposal in landfill can be hazardous. It makes economic and environmental sense to recover materials from end-of-life products, like batteries and printed circuit boards (PCBs). Even at a household level, we can identify things like electronic components, batteries, from consumer devices up to electric vehicles, and catalytic converters on cars that can all be recovered and reused. At an industrial scale, we are looking at items like spent industrial catalysts, solar panels, turbines and generators.
The good news is that there is a way to extract critical materials from spent devices and equipment, prevent hazardous waste reaching landfill, and create a beneficial by-product.
The answer lies in plasma technology.
Just as critical materials are initially mined from the earth, recovering materials from waste is a process. If we follow the journey of a PC past its usable life, for example. Its responsible owner takes it to the municipal household recycling centre or puts in a WEEE dumpster. Initial processing at a waste management centre strips and shreds the plastics and isolates key materials for extraction. The critical materials are concentrated in the remaining Printed Circuit Boards (PCBs) and can go through a controlled process where plasma technology is applied and the precious metals are recovered. Any spent materials are converted into substances that are benign to the environment.
Why plasma? Plasma is an electrically charged – or ionised – gas. It’s sometimes described as the fourth state of matter and occurs naturally in the environment in lightning, sparks from static electricity and the aurora borealis. Plasma is used in television and display screens, fluorescent lighting and even arc welding.
Tetronics uses plasma technology in an extensive range of applications from recovering precious metals to removing the toxicity of industrial materials like asbestos and air pollution control residues. To recover critical metals from electronic equipment, Tetronics’ process involves introducing the materials – in the PCB feedstock – into a sealed furnace and using a plasma arc to apply intense heat and ultra-violet light in a controlled environment. The chemistry separates and recovers the valuable metals, minerals and other materials from the feedstock. The process destroys any hazardous elements and leaves behind a non-hazardous glass-like material called Plasmarok. This itself is used as an aggregate in road paving and pipe bedding for the construction industry. Nothing is wasted. And, because it is powered by electricity rather than fossil fuels, it can be one of the cleanest thermal processing technologies available.
Using plasma technology to recover precious metals returns some significant financial benefits. Consider the mobile phone graveyard playing out in many a kitchen drawer: a YouGov survey of 2,000 UK adults showed that 67 per cent own one or more redundant mobile phones. Research commissioned by giffgaff suggests unused and recyclable mobile phones across the UK could be worth an estimated £3.4 billion. Overlay this with the UN’s Global E-waste Monitor report that says that only 20 per cent of e-waste is recycled, and the volume of recoverable resources being needlessly stashed or thrown away is astonishing.
As compelling as the financial and environmental benefits of critical mineral recovery are, there are other benefits to be had. It removes the risk to public health from dumped heavy metals like lead and cadmium, leaching into the soil and water table landfill sites. It prevents the exploitation of people in poorer economies who are used to source or recover materials in uncontrolled, unsafe, practices, and it reduces the opportunities for the illegal and dangerous trade in e-waste.
There could be a case for tighter legislation around recycling e-waste, but the intention to alleviate the pressure on primary supply outlined in the government’s policy paper is a good starting point. The need to promote innovation for a more efficient circular economy in the UK is being strongly reinforced by recovery specialists like Tetronics. We have the technology, the capacity and the desire to recycle more. It may take manufacturers and suppliers of mobile phones, laptops, batteries and many other electronic devices, to play a bigger part in encouraging consumers to recycle old equipment and release the value currently hiding away, untapped; whether inside our homes or parked in front of them.