How-To: Combat Unplanned Equipment Downtime
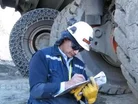
Operations need to run smoothly and economically with little or no downtime to be successful. Unplanned equipment breakdown can often be the most timely, and expensive, setbacks for mining companies.
The following infographic reveals the obstacles in unexpected downtime including associated costs and loss in productivity.
According to the infographic, mining companies are susceptible to $180,000 in lost production per incident. This includes lost production time accumulating in $3,000 an hour per incident, and 60 hours of downtime per incident.
The following tactics can significantly assist in combating unplanned downtime.
Comprehensive maintenance
Regular inspection and maintenance of equipment is pivotal to minimizing downtime. It eliminates unexpected repairs and replacements as well ensuring machinery is top-notch and running correctly.
Keep accurate record
After each routine check, a comprehensive report should be conceived with detailed cost analysis. This will allow mining companies to control and monitor the wear rate of equipment, helping to prevent unplanned breakdowns and repairs.
Put a predictive plan in place
Mining equipment is the lifeblood to any successful operation. According to the infographic, 47 percent of downtime is contributed to hydraulic power and belt drive failures. To prevent this, put a plan in place.
By maintaining regular maintenance and accurate record of mining equipment, companies can implement a 'plan of action' in case unexpected problems on the job site occur.