MMG’ Dugald River Mine Investigates Tyre Recycling Programme
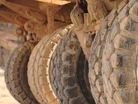
MMG, the operator of the Dugald River underground zinc mine, is experiencing a considerable task. The company is currently strategising to meet the ban on used tyre exportation, which was set by the Council of Australian Governments and is due to take effect in December 2021.
This is an important measure for the country, as it aims to tackle the growing number of waste tyres by more sustainable means. According to Energy Estate - a global advisory firm, Australia disposes of over 60,000 tonnes of end-of-life (EOL) tyres by exporting them, but it still faces a stockpile of around 100,000 tonnes - the majority of this is from the mining and agricultural sectors.
Currently, the Dugald River mine generates 920 EOL tyres from heavy industrial vehicles. With the ban on tyre exports looming, the mine is working with its contractor, Barminco, to come up with a more sustainable way to dispose of tyre waste. The mine now supports a programme called ‘Reviving End of Life Tyres’ (REVYRE), which is a joint venture with the Energy Estate and InfraCo.
The programme supports a circular economy by separating and reusing the components of EOL tyres. The byproducts of the recycling process will provide high-value polymer products for use in tyre manufacturing and producing clean tensile scrap steel.
How Will The REVYRE Programme Remain Sustainable?
REVYRE describes the process as “chemical and solvent-free with near-zero waste and emissions or byproducts making it an environmentally friendly technology” and is also looking to power the recycling operations with renewable energy, aligning the project with its low carbon footprint strategy.
There are a number of REVYRE recycling plants planned, of which there will be one for each Australian mainland state. The implementation of these plants will support the creation of jobs throughout all aspects of developing the sites, construction of the plants and the general operations - with the potential to further reduce CO2 emissions from EOL tyres.
How Does The REVYRE Process Work?
The process of recycling EOL tyres through the REVYRE programme follows true circular economy principles, putting tyre compounds back into the production line. The solution involves separating the rubber and steel components of the tyres and converting them into usable forms. Some of the applications for the recycled rubber include new tyres, work boots and rubber machine components like belts. The steel component can be reused in various steel shapes as well. The process uses devulcanisation equipment, developed by Tyromer Inc., which produces rubber granules into Tyre Derived Polymer (TDP).
REVYRE has explained the process is the “only true circular economy rubber resource recovery process available that brings together two award-winning tyre recycling technologies for the first time.” It also states it “does not alter the beneficial material properties of the rubber or steel and does not degrade or dematerialise those materials.”