Thermo Fisher Scientific Tackling Lithium eco Issue
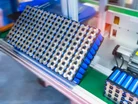
Every industry is searching for ways to increase its sustainability credentials, to win the favour of customers and stakeholders.
The irony is that while electric vehicles (EVs) can lower carbon emissions, decrease air pollution and support the circular economy, its batteries – the heart of the vehicle – are not sustainable.
Lithium-ion batteries require mining for lithium and nickel, processes that can lead to soil and water pollution.
Every tonne of mined lithium results in 15 tonnes of CO2 emissions, and an estimated 500,000 litres of water is needed to mine around 2.2 million litres per tonne of lithium. This substantially impacts the environment, leading to water scarcity in already arid regions.
Also, much of the world’s cobalt, another component of lithium-ion batteries, is sourced from mines in the Democratic Republic of Congo, which has been accused of poor working conditions and child labour.
As a result, scientists are developing new chemistries for batteries, by using more common, and less expensive, materials.
Dan Shine, who is President of Analytical Instruments at Thermo Fisher Scientific, says the company is trailblazing advances in sustainable EV initiatives
Battery science looking to replace lithium with sodium
“Researchers are exploring the use of sodium-based batteries to replace lithium-based batteries,” he says. “By using a more common and affordable element, sodium-based cells could help alleviate environmental stressors.
“Utilising AI and other new technologies, we are focused on driving the cutting edge of analytical technology in the lab and supplying end to end solutions that support numerous fields of study with greater ease and usability.”
He adds: “We’re working to create technological solutions to help researchers advance the battery industry and resolve today’s toughest problems and future needs.
“Our electron microscopes are a principal tool helping to advance battery science and engineering.
“We believe that investments in battery R&D will remain strong in the next decade – and not only in universities and academic knowledge centres – but also in battery manufacturing, government and private sectors.
”We’ve already seen heavy investments in battery research and development to advance technology and address global challenges, like the adoption of clean energy solutions, expansion of electric vehicle batteries and safer disposal and recycling of batteries.”
He adds that many researchers are looking at more-common materials, like sodium, to improve battery life and make battery manufacturing more sustainable.
“Low- and mid-nickel nickel-manganese-cobalt variants are beginning to phase out, while lithium ferro-phosphate has re-emerged due to reduced cost, higher safety and improvements to packaging design,” Shine explains.
- Albemarle Faces Billion-Dollar Loss Amid Lithium Price DropSupply Chain Management
- Rio Tinto to Acquire Arcadium Lithium for $6.7bnSupply Chain & Operations
- Rio Tinto eyes Arcadium Lithium in Battery Metals MoveOperations
- Albemarle & SWA Benefit From $3bn US Battery Production CashSupply Chain & Operations