How Soter Analytics captures and analyses data to prevent human breakdown in mining
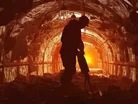
Soter Analytics develop wearable health technology for the industrial workforce. The resources tech startup is a foundation member of CORE Innovation Hub, having been based at CORE since its opening in October 2016.
In our two-part feature, Matthew Hart, CEO and Founder, explains how the company's SoterSpine™ solution answers a key industry problem, what challenges it has faced as a hardware startup and the plans for the future.
Can you briefly describe your industry solution and the problem it is solving?
We develop wearable health technology for the industrial workforce, as we strongly believe that injuries will be eliminated with the insights that come from the data we collect and analyse. The SoterSpine™ is a wearable device and app that helps industrial workers by reducing preventable musculoskeletal injuries. It identifies and quantifies musculoskeletal risk, gives instant feedback to the worker if they make high risk movements, and then our AI health coach provides personalised training the worker on how to further reduce their injury risk.
How did Soter Analytics come about?
I used to be a Reliability Engineer and then a Productivity Analyst for BHP and dealt with operational productivity challenges on a day to day basis.
Around this time, I travelled to Russia and became particularly interested in St Petersburg. Over the next few years of travel I realised that there is a huge tech talent pool in St Petersburg, where I first met my Co-Founder Alexey Pavlenko at a Finnish startup pitching event called Startup Sauna.
I was pitching a fleet management system and Alexey was pitching another idea about on-demand car washing. Over the next 6 months, we got to know each other, became friends, and he sought to help me, with developing my first fleet management system idea.
It all ended up being just a bit too hard, so we turned to our second idea; safety wearables idea and it's been a pretty good strategy.
In my role as Reliability Engineer, I took data from machines to figure out when they were going to break down, and then stopped that breakdown from happening. This data is processed in different ways and then you derive actionable insights from that. I also used that same data for productivity analysis; looking at the lost productivity and then putting in solutions to stop it happening again.
This lead us to think: why don't we do that for people? People are just really complex machines. Why don’t we put a sensor on a person, nobody has really done it before? Let's capture data that stops the breakdown of a person.
We ended up building a concept together, and then brought that to our customer Roy Hill. I pitched it to them, and they were happy with it and agreed to support us while we built the MVP (Minimum Viable Product) versions, prototype versions, and to date we've done three trials with them. We have more business planned and the relationship continues to grow.
How do you see the SoterSpine entering the supply chain? Does it have an application beyond the energy resources sector?
The SoterSpine will be available as a solution ready for easy implementation in July. We have three enablers for this. The first is that our solution works. On-site testing has delivered a reduction in the amount of high-risk movements by up to 70%, so we can make a big impact on the workplace. The second enabler is the low cost of the product, and the third is its easy implementation.
It’s effectively plug-and-play, so employees can set it up themselves in under a minute, clip it on and go. The SoterSpine can be used in any industry where people undertake manual tasks. We have existing and potential customers from the mining industry, and trials scheduled in the energy industry in Western Australia and Queensland, and in the construction sector in Belgium and the United Kingdom.
What are the major challenges you have faced as a hardware startup? How have you overcome them? Any advice for startups in hardware?
Building hardware is extremely challenging. The hardest thing we have found is the manufacturing process. Getting quality manufacturing when you're wanting to produce small batches of a new design that's never been done before is very challenging.
The whole process around building your supply chain is difficult to manage: getting components to your manufacturer on time, getting the device back from the manufacturer on time, getting the devices to your customers on time, etc.
We had a trial with Roy Hill late last year where the Bluetooth in our hardware device just wouldn’t work and a lot of our solution is built around transmitting data and then processing the data. So, we had all our devices, but none of the hardware worked as expected.
We could still download the data manually, but we didn't have that real time Bluetooth transfer, because it needed to be re-flashed, or reinstalled and we hadn't put any connections in our design to connect the Bluetooth to be re-flashed.
We've had other problems where components weren't attached properly due to poor manufacturing. We use a lot of new components in our device because we've designed it in a way to have a very long battery life. Because they were new components, our manufacturer wasn’t used to working with them and they made mistakes with attaching these components to the board. Therefore, at a certain point last year, we were manually soldering components to the board ourselves; taking them off, and then putting them back on.
However, all these challenges, all these steps we went through, ended up giving us the ability fail fast, learn from the experience and come out the other side stronger than before. We secured our first customer, we did trials with our MVP, and we built our own hardware. It wasn’t all plain sailing, but we got investors on board because they saw that we were making progress and we were getting our solutions to start working and that investment has now allowed us to bring a hardware designer in-house.
My advice would be to avoid making hardware for as long as possible, until you know exactly what you need. When we started, we were going to have a smartwatch and we realised that third party hardware wasn't going to be the perfect solution for us because the battery life was too small, and it was running too many things that we didn't need. At the very beginning we got a quote to build our own smartwatch. Imagine if we had actually built this, we didn’t end up needing one! So, yes, avoid building it for as long as possible. Hack third party hardware, find third party sensors or the equivalent for whatever you're working on until you realise what you want and are at the point where you are confident in designing your own.
TOMORROW: Don't miss part two to find out more about how working with the CORE Innovation Hub has played a significant role in driving true growth for Soter Analytics,