How technology can effectively manage and improve fatigue in mining
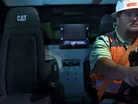
Data doesn’t lie.
According to recent studies, approximately 90 percent of accidents in the mining industry occur from human error. The majority of these accidents, which typically occur from mining machinery, are the result of driver fatigue and distraction.
For mining companies, there are direct and indirect consequences from fatigue. Direct effects include: lower productivity; equipment damage/premature maintenance, property damage; and fatalities, injuries and related expenses (lost time, medical expenses, workers compensation, legal expenses and regulatory fines). Indirect consequences may include everything from incident investigations, absenteeism to change in morale, higher turn-over rate and health, sleeping disorders.
Without a doubt, technology-enabled solutions have the ability to change that by monitoring, predicting, measuring and reducing fatigue events.
Caterpillar’s Fatigue Practice Manager Todd Dawson, a fatigue science expert with 20 years of experience building Fatigue Risk Management Systems, recommends three technological systems that will make immediate improvements to fatigue and distraction levels on site.
Fatigue Avoidance Scheduling Tool (FAST)
One of the many tools used by Rio Tinto, FAST is a software system used to analyze specific schedules to determine vulnerabilities. It generates graphical predictions of performances along with tables of estimated effectiveness scores for objective comparison.
Developed by Fatigue Science, this wrist-worn device automatically detects an employee’s sleep and wake periods and converts data into an effectiveness score. Using Caterpillar’s Smartband system, supervisors can review sleep and performance data for employees, filtering by specific groups and dates.
• Related content: [VIDEO] Improving fleet management with Caterpillar's MineStar technology
With data from the smartband, mining companies can incorporate it into the Fatigue Avoidance Scheduling Tool to get a clear vision of their current state, as well as tools to help managers schedule workers for increased safety and performance.
Used primarily in Caterpillar’s MineStar technology, DSS is a non-intrusive way to manage safety in real-time. It uses a camera, which is embedded in the vehicle, to detect a driver’s pupil size, how frequently they blink and how long they keep their eyes shut. It also monitors the driver’s mouth in order to analyze when the driver is distracted and not looking at the road.
The purpose of DSS is to detect the onset of micro-sleep – fractions of seconds where a person has fallen asleep without realizing it. When micro-sleep is detected, an alarm will sound and the driver seat will shake, sending visual recordings to a monitoring center that will review the situation. IF fatigue is detected, the monitoring center will notify a supervisor at the mine-site.
The system has been installed in over 5,000 Caterpillar trucks, recording roughly 6,000 fatigue events and 1.5 million distraction alerts. The results are frightening. According to Caterpillar, over 1,641 miles have been traveled while drivers were asleep.
Although technology has the ability to significantly improve accidents among miners, it’s not a one-stop shop solution.
According to Dawson, the key is an effective Fatigue Risk Management System (FRMS), which utilizes multiple layers of protection to minimize the risk of fatigue hazards becoming incidents.
“The Fatigue Risk Management System process is most effective when deployed in the sequence Engage, Assess, Define, Develop, Implement and Check. Each phase can also be used individually to help you reach specific goals.”
The system concentrates on having a process to identify the problem, fitting the solution to the problem (behavioral, physiological, operational) and managing the change (educating all involved parties, having clear prcedures for outcomes, follow up and improve).
• Related content: Caterpillar: How to ensure the successful deployment of autonomous haulage
Todd Dawson leads a team of Caterpillar safety culture consultants who work alongside customers to develop operational excellence through safety improvement. Over the past 20 years, Todd has become one of the leading experts in developing and implementing comprehensive fatigue risk management systems in large, complex environments. He has played an integral role in shaping the landscape of fatigue management, particularly in the transportation, mining and oil/gas industries.
Stay connected! Follow us on Twitter and like us on Facebook