Industry Q&A: Innovation through big data and equipment utilization
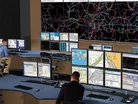
RungePincockMinarco are a major event partner of Austmine 2015: Transforming Mining. With the overarching theme of the conference being Innovation, it seemed an ideal time to catch up with their CEO, Richard Mathews, about how RPM strives for innovation, plus receive his insights into two of mining companies' greatest focuses right now: big data analytics and optimizing equipment utilization. Richard has more than 20 years' management experience in telecommunications, software and investment, with extensive knowledge of the mining and technology space.
As an Australian METS company, who are recognized in the industry as the world leaders in innovation and technological advancement, how important is it to keep innovating and collaborating within the industry as a whole to ensure its future? How does RPM drive innovation within its own business?
Innovation is the key to success in our industry, we have created some incredible products over the years, but if you rest on your laurels in the technology world you will die a quick death. The technology sector moves at such a pace, that without continual innovation your competitors move past you and your customers move away for you. In the mining industry, the fluctuation in commodity prices and the challenges that brings means there is a constant need to work smarter, increase efficiency and have better control over your operations. RPM have always taken the approach of working closely with its clients to ensure that our software is delivering exactly what the industry needs. Collaboration with miners is vital for delivering products that solve real world problems. Collaborating with industry partners is also important, in recent years RPM has been working closely with our partner SAP to the point where RPM’s enterprise connectors that integrate with SAP have been certified by SAP. Seamlessly connecting technical mine applications with corporate ERP systems is a step change for the industry.
• Related content: Caterpillar: How to ensure the successful deployment of autonomous haulage
At RPM we have an expanding team of talented software developers, we have a collaborative approach to problem solving and everyone is encouraged to share ideas and test theories. We mix that development skill with in-depth knowledge of mining practices from our advisory division. We have some incredibly experienced and knowledgeable people that work closely with our customers to drive the functionality of our products. We have created an environment where people come up with ground breaking ideas and we invest in those ideas for the benefit of our customers.
What do you see as the biggest opportunities for the mining industry in Australia in 2015 to improve productivity?
We believe that the best way to drive down the cost of mining is through the introduction of technology solutions that optimise the mining supply chain from the mine plan all the way through to delivery of the customer product. Sharing information between interested parties visually means everyone is on the same page. Clear communication removes the natural conflicts of interest and silos between departments and ensures that previously wasted time and effort, repetition of work and errors are removed for the operations of the business. The ability to optimise, simulate and cost out mining plans before they are put into action inherently drives down the cost of mining.
There’s a lot of talk around big data in the mining industry currently, and a big part of this is of course down to system selection and integration and the ability for systems to communicate. What are the biggest pitfalls you see mining companies falling into when upgrading systems, or looking to get the most out of their platforms?
Integration is a must, but mining companies haven’t always had a choice, historically they have had to use a range of disparate systems spanning a variety of departments to do their planning. Moving forward, having applications that talk to each other and are seamlessly integrated is going to be essential for success. Miners need systems in place that eliminate manual manipulation of data, remove data file transfers and anything that creates a risk of errors occurring. Having a fully integrated enterprise suite of planning products that are connected to the corporate ERP is the way of the future. It breaks down silos, encourages collaboration and provides the opportunity for users to spend more time analyzing data rather than creating it and shuffling it around between different systems.
Another focus area for many miners right now (e.g. Centennial Coal) is on really optimizing equipment utilization. Do you have any tips for miners looking to improve this on their sites?
Equipment, both the capital expenditure and the operating cost is the biggest expense for any mining operation, so optimizing a fleet is crucial for getting the most value from that investment. RPM believes that enabling clear visibility of the real operational requirements for equipment is essential. Visibility then enables informed decisions to be made about how a fleet could and should be used. This can be done through simulation and scenario analysis.
Product simulation software using TALPAC has been part of the RPM DNA for over 30 years, but the last 18 months has seen some incredible advancement in this area.
• Related content: Mining Global Magazine I May Edition
Discrete event simulation is a big focus for RPM right now. Delivering a platform in which miners can map their entire haulage and loading systems means that theories can be tested and a variety of options can be explored before any spend is committed. RPM has developed HAULSIM to provide that solution for RPM clients. We have had a fantastic response to HAULSIM since its launch, as the value it provides a mining operation is obvious almost immediately. Being able to realistically simulate mining operations before you actually start means you can identify any bottleneck before they start costing you money. Building an optimized equipment fleet through the use of scenario simulations again drives down the cost of mining - often for a very low investment cost.
My tip would be to look at ways to explore all of your equipment decisions and haulage options before you make them, test your theories and be certain that you are making the best decision before you move a single truck!
- Mining machinery market analyticsTechnology
- How TOMRA’s tech is boosting productivity at Peru’s San Rafael tin mineDigital Mining
- Caterpillar R2900 Underground Loader meets emissions standards for global minersDigital Mining
- Seven Group Holdings sells Chinese mining machinery arm to Lei Shing Hong for $428mnAutomation & AI