Robots Could Radically Transform Mine Safety, Experts Say
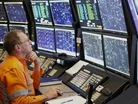
Robotics and remote technology could transform one of the world’s most labor-intensive and potentially dangerous industries. The mining sector is notoriously hazardous due to the nature of the sector, however the introduction of robots, drones, driverless trucks and pilotless trains could transform mine safety. A technology boom could also allow for the development of mines in regions once thought too precarious or remote to exploit.
Rio Tinto is a leader in this field, funding one of the world’s largest non-military robotics programs, which will soon use unmanned trains to deliver cargo to the coast and set drones aloft at its remote mines. John McGagh, head of innovation at Rio Tinto is confident that come October 2014, drones will be operational at mine sites, monitoring stockpiles, mapping exploration targets and tracking equipment.
Watch the video below to understand what Rio Tinto is doing to enhance safety using robotics and technology:
Mining without miners
Rio Tinto is not the only mining powerhouse about to utelise drones and remote technology on site. BHP Billiton and Anglo American are also ramping up efforts to automate, believing that new equipment will cut costs and improve returns, while allowing them to exploit deposits so far considered too complex or too dangerous for humans. It’s also thought that technological advances could pave the way for a new generation of mines, located in extremely remote locations. Rather than having a human presence on the ground, operations will be conducted from afar in high-tech control rooms.
The insertion of remote controlled technology brings direct health and safety benefits by allowing miners to perform the same task without having to be within close proximity of potentially hazardous environments.
“Reducing the numbers of people involved on the field mechanically reduces the probability of having accidents, especially considering that the mining industry will extract commodities from deeper and more complex ores in the future,” says Philippe Dozolme, a mining and explosives specialist, writing for International Mining magazine. “By providing a safer working environment, the mining industry might be able to tackle the current labor shortage and attract high potential profiles.”
Reducing the risk of human error
Furthermore, by replacing a workforce on the ground with more predictable and precise remote controlled automated equipment, the likelihood of human error is reduced dramatically. On top of that, sensors and diagnostic tools that are incorporated in such equipment allow problems to be picked-up earlier, reducing maintenance costs and downtime.
Removing the human element from mine sites is undoubtedly good for reducing risk, however the benefits extend far beyond health and safety. While there are no set-in-stone estimates regarding the cost saving benefits of remote technology, there are hints based on current applications of smart tech. For example, Rio Tinto’s use of sensors to fine tune copper processing has seen free cash flow increase by $80 million over the course of a year, according to CEO Sam Walsh. Since taking the helm of the company in January 2013, Walsh has reduced costs company-wide by $2.3 billion.
If managed correctly, automation and robotics can dramatically reduce risk in the mining sector, ultimately leading to a safer and more efficient mine site.
- Rio Tinto to Acquire Arcadium Lithium for $6.7bnSupply Chain & Operations
- Rio Tinto, BHP & Glencore 'Feeling the Pinch on Copper'Supply Chain & Operations
- Rio Tinto Brings Simandou Guinea Iron Ore Saga to EndOperations
- Exyn Nexys: a 3D Mapping Instrument for Mining ProfessionalsTechnology