Sandvik Looks to Utilize 3-D Printing in Mining Equipment
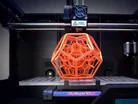
As 3-D printing continues to skyrocket in popularity, appealing to numerous industries around the world, one mining equipment manufacturer is putting the technology to use.
Sandvik, the world’s largest maker of metal-cutting tools, announced it will boost research spending on 3-D printing to expand capabilities in a market that is expected to grow to $21 billion in the next 10-years.
From mining drill rigs to fuel tubes for nuclear power plants, Sandvik will evaluate the technology through various initiatives to observe how the technology can be used in its production. Sandvik is opening a new 3-D printing research and development center in Sandviken, Sweden and is preparing to hire a team for the center.
“We’re taking this to another level,” Schuisky said. “We’re making a focused strategic push to research this for the benefit of the entire group.”
Somewhat similar to additive manufacturing, 3-D printing is a process of making three dimensional solid objects from a digital file. The process enables faster production, increased flexibility and the ability to shape otherwise impossible designs from standard methods.
’’What is attractive about 3-D is the new way of thinking,’’ Schuisky said. ’’We are used to thinking that objects are processed out of a material. We need to start thinking about starting from a blank canvas.’’
While the implementation of 3-D printing sounds exciting, there are still question that need to be answered. Case in point: production times.
“You can punch out objects so much faster using those traditional technologies. And I don’t see that changing,” IDTechEx Director Jon Harrop told Bloomberg. ’’I only see it really having an effect on small, high-value components.’’
Still, the case for 3-D printing in the mining industry is compelling. Because most mining operations are located in remote areas, companies would be able to make their own parts on site in a fraction of the time it takes to get parts sent in.
“It’s like Batman’s utility belt, to get through his day he needs to be able call on a number of different technologies or a number of different tools,” says mechanical engineer, Simon Bartlett.
“I think it’s definitely a new tool and people are now just trying to work out how it fits in to what they do.”