Predictive Maintenance Reshaping Mining Operations
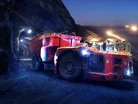
Predictive maintenance (PM) is transforming the mining industry by optimising equipment performance and reducing downtime. This approach uses data analysis and machine learning to forecast when maintenance is needed, preventing unexpected failures.
PM is applied to a wide range of mining equipment, from haul trucks and excavators to conveyor belts and crushers. These machines are fitted with sensors that continuously monitor various parameters such as temperature, vibration, and oil quality.
The technology behind PM involves Internet of Things (IoT) devices, cloud computing, and artificial intelligence. Sensors collect real-time data, which is then processed and analysed to identify patterns and anomalies that may indicate impending equipment failure.
Multinational mining company Anglo American has implemented PM across its global operations, using IBM's Maximo Asset Management system to monitor the health of its mining equipment.
This system has helped Anglo American reduce unplanned downtime by up to 75% in some of its operations. It has also improved equipment reliability and extended the lifespan of critical assets.
Sandvik & IBM tap power of IoT
IBM and Sandvik Mining, meanwhile, are tapping the powers of IoT, advanced analytics and AI to realise safety, maintenance, productivity and operational efficiency.
The mining and rock excavation industry is under growing pressure to increase the global supply of minerals to meet the needs and expectations of a rapidly rising world population. This often requires extracting from increasing greater depths, which can make it difficult to communicate and act as necessary when equipment fails or needs to be serviced.
OptiMine Analytics transforms data into process improvements via predictive insights and actionable dashboards embedded into operation management systems. Using the analytics capabilities from IBM Watson IoT, this information management solution allows mining companies to combine equipment and application data from disparate sources in real-time, analysing patterns in the data to help improve availability, utilisation and performance.
IBM and Sandvik work with clients to develop a framework to shape offerings around data driven productivity and predictive maintenance.
Using the Watson IoT technology, Sandvik and IBM have jointly created a platform able to comply with the stringent reliability and security requirements of mining operations. Predictive maintenance technology leveraging IoT sensor data has also been introduced as part of this platform.
“Proactively identifying maintenance needs before something breaks is leading to huge cost and time savings,” says Patrick Murphy, President, Rotary Drilling at Sandvik.
“Our award-winning OptiMine Analytics with IBM Watson IoT solutions offer our customers a more complete view of their operations for smarter, safer and more productive work,” he adds.
Petra Diamonds & Barminco use IoT to keep miners safe
Sandvik and IBM clients include Petra Diamonds and Barminco, who use IIoT to help reduce miner exposure to hostile work environments and increase safety.
“Our top priority is the safety of our employees and if a machine fails underground we need immediate insight into what is happening in that tunnel,” says Luctor Roode, executive operations at Petra Diamonds. “With the solution from Sandvik and IBM, we have real-time data that allows us to immediately identify the root cause of the problem and act accordingly.”
“Leveraging data is become increasingly valuable across the mining sector. Through analytics, machine learning and AI, we are seeing new possibilities for increased operational efficiency,” said Paul Muller, formerly CEO of Barminco, and now Chief Executive of diversified Australian mining services group, Perenti.
“Our partnership with Sandvik’s OptiMine Analytics allowed us to fast-track our efforts, leveraging Sandvik’s whole-of-fleet data and innate machine knowledge,” he added.
Newmont's GE Digital solution enhances safety
Newmont Corporation, one of the world's largest gold producers, has also embraced PM. The company uses GE Digital's Asset Performance Management (APM) software to monitor its mining equipment.
Newmont's APM system analyses data from thousands of sensors across its operations. This allows the company to predict potential equipment failures and schedule maintenance proactively.
The implementation of PM has not only improved equipment reliability but also enhanced safety at Newmont's mining sites. By preventing unexpected breakdowns, the risk of accidents related to equipment failure has been significantly reduced.
Vale, a Brazilian multinational mining company, has implemented PM in its iron ore operations. The company uses IBM's Watson IoT platform to monitor its conveyor belt systems.
Vale's system uses acoustic sensors to detect anomalies in the conveyor belts' operation. Machine learning algorithms analyse the sound patterns to identify potential issues before they lead to failures.
This PM approach has helped Vale reduce unplanned downtime in its conveyor systems by 30%. It has also improved the overall efficiency of its iron ore production process.
Smaller mining companies see tech benefits
The adoption of PM in the mining industry is not limited to large corporations. Smaller mining companies are also recognising the benefits of this approach.
For example, Dundee Precious Metals, a Canadian-based international gold mining company, has implemented a PM system at its Chelopech mine in Bulgaria. The company uses OSIsoft's PI System to collect and analyse data from its mining equipment.
This system has helped Dundee Precious Metals improve its overall equipment effectiveness by 20%. It has also reduced maintenance costs and improved safety at the Chelopech mine.
As PM technology continues to evolve, mining companies are exploring new applications. Some are experimenting with drone-based inspections to complement sensor data.
Others are investigating the use of augmented reality for maintenance tasks. This technology could allow technicians to access real-time data and instructions while working on equipment.
The mining industry's shift towards PM reflects a broader trend of digital transformation. As companies continue to invest in these technologies, the benefits are likely to extend beyond equipment maintenance.
PM data can provide insights into operational efficiency, energy consumption, and environmental impact. This information can help mining companies optimise their processes and improve their sustainability performance.
The benefits to supply chains of Internet of Things (IoT) technology are substantial, and include increased visibility, more collaboration, better customer service and real-time tracking of goods.
----------------
Mining Digital is a BizClik brand