Rio Tinto, BHP Reap the Benefits of Mining Automation
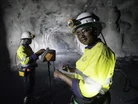
The mining industry is undergoing a significant transformation through automation. From prospecting to mineral processing, technology is helping companies enhance productivity, safety and sustainability.
This shift is reshaping operations across the sector, with major players like Rio Tinto and BHP at the forefront of innovation.
In prospecting, automation has improved the accuracy and speed of mineral exploration. Drones equipped with advanced sensors and imaging technology can survey large areas quickly and efficiently. These unmanned aerial vehicles collect data on geological formations and potential mineral deposits, reducing the need for costly and time-consuming ground surveys.
Machine learning algorithms analyse this data to identify promising sites for further exploration. This technology allows mining companies to make more informed decisions about where to allocate resources, increasing the likelihood of successful discoveries.
Rio Tinto's autonomous haulage system
Building mining infrastructure has also benefited from automation. Computer-aided design and building information modelling streamline the planning and construction process. These tools enable engineers to create detailed 3D models of mine sites, optimising layout and resource allocation before breaking ground.
Automated construction equipment, such as self-driving bulldozers and excavators, can work around the clock to prepare sites for mining operations. These machines use GPS and sensors to navigate and perform tasks with precision, reducing human error and increasing efficiency.
In overground mining, autonomous haulage systems have revolutionised operations. Rio Tinto, a leading global mining group, has implemented a fleet of driverless trucks at its iron ore mines in Western Australia. These vehicles operate 24/7, transporting ore from the pit to processing plants without human intervention.
The autonomous haulage system has improved safety by removing drivers from potentially hazardous environments. It has also increased productivity, as the trucks can operate continuously without breaks. Rio Tinto reports that these autonomous trucks are up to 15% more efficient than manned vehicles.
Underground mining presents unique challenges, but automation is making inroads here as well. Remotely operated drilling rigs and loaders allow miners to control equipment from a safe distance. This technology reduces the risk of accidents and exposure to harmful dust and gases.
BHP, one of the world's largest mining companies, has implemented autonomous drilling systems at its iron ore mines in Western Australia. These systems can operate multiple drill rigs simultaneously, increasing drilling efficiency and accuracy.
BHP's automated processing plants boost efficiency
In metals and mineral processing, automation has led to significant improvements in efficiency and quality control. Automated sorting systems use optical and X-ray technology to separate valuable minerals from waste rock. This process increases the purity of the final product and reduces energy consumption in downstream processing.
BHP has implemented automated processing plants at several of its operations. These facilities use sensors and control systems to optimise crushing, grinding, and flotation processes. The result is improved mineral recovery rates and reduced operating costs.
Automation in mining extends beyond equipment to encompass entire operations. Centralised control rooms allow operators to monitor and manage multiple sites from a single location. This approach improves coordination and decision-making across the mining value chain.
Anglo American's FutureSmart drives innovation
Anglo American, the multinational mining company, has launched its FutureSmart Mining programme to drive innovation across its operations. This initiative focuses on developing and implementing advanced technologies, including automation, to improve safety, sustainability, and productivity.
The programme includes projects such as autonomous drilling and bulk ore sorting. These technologies aim to reduce energy and water consumption while increasing mineral recovery rates.
Automation in mining offers numerous benefits, including improved safety, increased productivity, and enhanced sustainability. However, it also presents challenges, such as the need for workforce reskilling and significant upfront investment.
As the industry continues to evolve, mining companies must carefully consider how to integrate automation into their operations. Those that successfully navigate this transition stand to gain a significant competitive advantage in an increasingly complex and demanding market.
Mark Cutifani, Chief Executive of Anglo American, emphasises the importance of embracing automation: "The future of mining lies in our ability to harness technology and innovation. Automation is not just about replacing human workers; it's about augmenting our capabilities and creating new opportunities for growth and sustainability."
Featured Articles
A fleet of Huaneng Ruichi autonomous electric mining trucks have been deployed in China, supported by Huawei's Cloud Services and 5G-Advanced network
Rio Tinto completed its US$6.7bn acquisition of Arcadium Lithium, making it a key company in raw materials mining for batteries in the energy transition
Intel first began to work towards responsibly sourced conflict minerals from the Democratic Republic of Congo and adjoining countries about 12 years