Mining Automation Drives Efficiency and Safety Gains
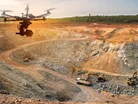
In recent years, drilling technology in the mining industry has moved on apace, with several solutions emerging to address key challenges. Here, we explore some of these tech breakthroughs.
Automated drilling rigs
ADRs are revolutionising mining operations by reducing labour costs, increasing efficiency, and improving safety.
These rigs require fewer workers to operate than conventional equipment and offer benefits such as reduced downtime and more efficient exploration.
ADRs incorporate artificial intelligence (AI) and machine learning capabilities to optimise equipment performance. This technology helps reduce maintenance costs and improves worker safety by minimising human exposure to hazardous environments.
Companies such as Komatsu, a Japanese mining equipment manufacturer, are at the forefront of developing automation-ready drilling equipment. Their systems can automatically adjust drill bit speed and pressure based on rock formations encountered.
Drone-assisted exploration
Drones is another innovation area transforming the mining industry. Drones can survey areas above or below ground more quickly and safely than traditional methods involving helicopters and ground teams.
RocketDNA, a drone technology company, offers "drone-in-a-box" solutions that allow mine operators to efficiently survey target areas and gather critical geological data. These systems operate autonomously with minimal human intervention.
Sustainable drilling practices
This is becoming increasingly important as the mining industry seeks to reduce its environmental impact. Electrification of equipment and processes, powered by renewable energy, is a key focus for many mining companies.
Portable drilling rigs that can be easily transported to remote locations are helping to reduce carbon emissions and minimise ecosystem disturbance. The industry is also exploring energy-efficient rigs and water-recycling systems.
Deep-sea mining
This is emerging as a potential source of critical minerals needed for the energy transition. However, this practice faces significant regulatory hurdles due to concerns about its impact on marine ecosystems.
Companies are developing specialised equipment for seabed mineral collection, including robotic mining vehicles and lifting systems. These must be designed to withstand extreme pressures and operate in remote locations.
Real-time monitoring of mining equipment
This is crucial for optimising performance and safety. IoT-enabled sensors feed data to central hubs, where it is analysed to inform decision-making processes.
This enhanced monitoring capability improves rig performance, mineral extraction efficiency, and worker safety. It also contributes to improved financial performance in a volatile market environment.
Major mining equipment manufacturers like Epiroc, a Swedish company, are integrating data analytics and AI into their drilling systems. These technologies help optimise rock fragmentation and improve overall operational efficiency.
Orica, an Australian explosives and mining services company, has developed automated charging systems for explosives. These innovations improve safety by reducing the need for workers to handle explosives directly.
ABB, a Swiss-Swedish multinational corporation, has created a robotic system for installing explosive charges in rock faces. This technology further reduces human exposure to dangerous mining environments.
Despite these advancements, the mining industry faces ongoing challenges related to environmental impact, geopolitical risks, and regulatory pressures. However, continued investment in technology and sustainable practices is helping to address these issues.
______________________________________
Check out the latest issue of Mining Digital and sign up to our global conference series, Manufacturing LIVE 2024. Mining Digital is a BisClik brand.