Vale’s robot rescue for Brazilian iron and copper operations
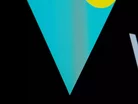
We’ve all seen the movies and know that the general consensus is that robots are destined to turn on us, but Vale seems determined to avoid that dystopian-esque vision and, instead, use the innovative technology for good. In an attempt to reduce the risks to its employees and assist in the maintenance of operations, the mining giant has adopted the use of robots to prove that this particular type of technology has a place in the future of the mining industry.
There are three main robot models currently being used by Vale in its operations, two of which have been developed by the Vale Institute of Technology (ITV), and a third - nicknamed by the company as “Puppy” - that Vale has procured from ANYbotics: ANYmal.
Vale streamlines mining operations by welcoming robots to the team
Developing robot tech isn’t a new novelty for Vale. Starting in 2010 and leading into 2015, the miner launched its SpeleoRobot project, created to cope with unpredictable terrain and, with high-quality cameras and lighting, aid speleologists in exploring caves in the vicinity of its nearby operations. Now deemed a valuable technological asset, the SpeleoRobot has gone on to be trialled in a number of different environments, including performing over 15 different operational services in the Brazilian states of Minas Gerais, Espírito Santo, and Pará.
Currently, the miner is working on developing three additional SpeleoRobots to be distributed to aid copper operations in Pará and iron ore operations in Vitória and Itabira.
But Vale’s robotic technology isn’t limited to just mining. Several of ITV’S robot perception modules have been eyed up by the likes of NASA, who are keen to learn from the technology being developed underground, and adapt it for its operations in space.
“These robots were created within Vale by the employees themselves and are a constantly evolving technology,” explains ITV researcher Gustavo Pessin. “Development is open-source, completely open from hardware to software, and its structure is modular. Everything that is developed can be used in other robots and equipment and adapted to new situations or functionalities using resources within Vale.”
Vale ventures into the future with robotic resources
On top of its own robotic innovation, Vale is equally as keen to acquire other technology, outside of that developed under its own name, to help expand its technological portfolio. ANYmal, created by Swiss company ANYbotics, has been modified to suit mining operations by Vale. Following successful trials at Itabira’s iron ore plant that saw the robot manoeuvre stairs and execute route planning, the mining company agreed to add the robot to its inventory, optimistic that ANYmal can help improve its operational efficiency and reliability.
“With the robot, we eliminate risks pertaining to inspection activities, such as rotating equipment parts, noise, and dust,” states Rayner Teixeira, Operational Analyst for Vale’s development of ANYmal. “We also eliminate activities that have ergonomic risk, where the employee would need to perform a task in an uncomfortable position.
“The robot also gives us access to confined spaces, like the inside of a mill.”
Vale is hopeful that it can lead the way in robotic innovation to enhance the future of mining safety and success. As a company, it’s never shied away from taking the first leap.
“Innovation is key for Vale to improve people’s lives and transform the future together with society. In its strategy, the company prioritizes safety, reliability, low carbon agenda and generation of shared value,” the company said in a statement.
“Ongoing safety innovation initiatives aim to remove employees from risk or reduce their exposure through the use of technologies such as autonomous vehicles, among others; identify and resolve causes of accidents with motor vehicles and energy equipment through operator fatigue detection systems and proximity alerts, for example; and elimination of risk scenarios.”