Promising results from Cyclic Materials' new Pilot Plant
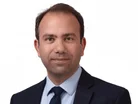
Rapid global industrialisation and population growth are placing increasing pressure on availability of raw materials. The group of elements known as the rare earth metals have become a sought-after resource for high-technology and low carbon industries.
Currently, global demand is increasing, expected to rise three-fold by 2030, and there are concerns over future availability. China has emerged as the dominant supplier of rare earths for various reasons. It has 35% of known world reserves, and has invested in the development of rare earth processing techniques since the 1960s. Also, it gave extensive state support to mining in the 1990s. Moreover until recently regulatory controls in China were relatively weak, which meant that Chinese producers were able to offer rare earths at low prices compared to competitors in other countries. This suppressed large scale development in other countries with known reserves. China currently supplies between 95-97% of global demand.
Sustainability in mining
Cyclic Materials' mission is to help the world transition to an environmentally responsible future by recovering rare earth elements from products that are difficult to recycle. This it aims to do by diverting material back into the supply chain to reduce the pressure to open new greenfield mines, improve the resilience of supply chains, creating jobs, and enabling new technologies by providing regional supplies of critical metals. On December 12 Cyclical Materials announced successful results from its new Kingston, Ontario pilot plant, where its proprietary Mag-Xtract technology isolates magnets from recycled end-of-life products. The design capacity of the plant is 1,000 kg/hour (8,000 tonnes per year), and initial runs have processed several tonnes of magnet feedstock per day.
“The launch of our pilot plant is a major step forward for developing a domestic, circular supply chain for critical materials at the scale needed to support the clean energy transition and technological innovation,” said Ahmad Ghahreman, co-founder and CEO of Cyclic Materials.
“Our magnet-agnostic recycling technology produces one of the cleanest and highest quality mixed rare earth oxide products available on the global market - an environmentally sustainable, first-of-its-kind solution to the limited international supply of critical magnet materials.”
In 2022, Cyclic Materials completed an initial proof-of-concept of Mag-Xtract, processing 4,000 kg of magnet-containing products—including copper, aluminium and steel— from end-of-life products. These materials are critical to the development of electric vehicles, wind turbines, smartphones and other technologies. In addition to developing Mag-Xtract, Cyclic Materials is scaling its proprietary hydrometallurgy technology to convert magnet feedstock and manufacturing waste into mixed rare earth oxide, cobalt-nickel hydroxide, and other by-products. Last fall, Cyclic Materials piloted its hydrometallurgy technology at a capacity of 10 tonnes per year. It is currently developing the first commercial demonstration plant for this technology in Kingston, Onario, with a target launch date in Q2 2024.
Cyclic Materials investors include BMW iVentures, Energy Impact Partners, Planetary Capital, Fifth Wall and Bio-industrial Innovation Canada, totalling over US$30m in funding raised to develop its advanced metals recycling processes. The company has also received a US$2.6m grant from Sustainable Technology Development Canada (SDTC).
**************
Make sure you check out the latest edition of Mining Digital and also sign up to our global conference series - Manufacturing LIVE 2024
**************
Mining Digital is a BizClik brand
**************