How-To: Implement Efficient Tailing Management in Operations
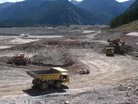
Most of the emphasis on operational efficiency and cost reduction is on the part of the production stream that extracts product for further processing and sale. The tailings department usually manages what’s left that cannot be sold. Consequently, there is often little focus on improving tailings management activities unless an event happens. Then all eyes are on tailings, especially if that event reduces or stops production.
Tailings are a critical step in the production flow. Without it, production stops. Many very different kinds of tasks fall under the tailings umbrella. Projects such as lifts require strong project management skills. Routine maintenance of valves, hoses and lines must be scheduled. The execution of preventive and quick-response dust control plans keep particulate levels below environmental limits. An in-depth knowledge of pump operations and slurry flow is required to “manage” deposition. To complicate matters further, every tailings management team must coordinate and simultaneously monitor all of these activities over a very large geographical area, sometimes miles across.
A common concern for tailings supervisors is knowing if each crew is doing what needs to be done to accomplish the goals of the department, especially if the supervisors are “roving”. So, how can a tailings department feel confident that they can effectively manage so many different kinds of tasks and meet their goals? One thing that I suggest is a plan for the day that is created by the supervisors in a joint meeting. This plan includes equipment status, shift rotations, 5000-23 qualifications, short term goals and long-term projects. Reaching agreement on a daily plan unifies the tailings management team and gives each supervisor a broader perspective of the work to be done and how crews will meet those goals. The plan can be constructed so that each supervisor can take a copy of it in his truck when the planning meeting concludes.
This portable plan greatly improves communications between supervisors and enables them to “co-manage” a large geographical area effectively.
About the author: Kay Sever is an industry leader in performance optimization and change acceleration. She helps companies experience “break-through change” by removing the barriers that hold them back. To assist with this work, Kay created a management training program that changes the way people think about change, their role in change and their beliefs about what is possible to change and achieve. It prepares companies for the optimization process and builds trust and management credibility.
- Brightstar, Eldridge and Claure acquire AusencoSupply Chain & Operations
- First Quantum contracts with MECS to cut emissionsSupply Chain & Operations
- Tin production at Andrada Mining reaches record levelsSupply Chain & Operations
- Ternium plans to build US$3.2bn steel plant in MexicoSupply Chain & Operations