The Mining Supply Chain and Ops
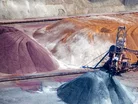
Supply chains and procurement operations have always functioned based on the proportionate connection between supply and demand. Thus, supplying raw materials that are high in demand, all parties in the supply chain generate profit. However, the recent disruptions in the ore mining industry could have repercussions that decide the fate of Electric Vehicles, aircraft engines, and wind turbines.
The Electric Vehicle industry, in particular, is expected to face a challenging roadblock due to an insufficient supply of lithium and other minerals. At the same time, the United States and the European Union have been pushing towards replacing fossil fuel-based machines with electric ones. Neither of these parties wants to keep relying on China, which has been controlling a substantial portion of processing minerals like lithium, cobalt, and graphite.
Amidst these geopolitical issues and the ever-increasing demand, the ore industry has to ask itself: is supply more important than cost?
Problems that Disrupt Mineral Supply Ops
For years, organisations have focused on industries that provide substantial profits by delivering supply to the sources that demand the same. Nevertheless, supply chain operations have to follow a unique strategy to align with the instructions from the governments and the big step towards eco-friendly business practices. To be more specific, organisations receive so much pressure towards creating a European supply chain for minerals that spearhead the development of EVs and other modern machines.
Before the pandemic started wreaking havoc across the globe, the industry was getting prepared for the upcoming boom of demand. It was predicted, among other things, that the EV industry would require more than 50% of the current global supply. Because electric vehicles use more copper than vehicles with an Internal Combustion Engine, the industry was left with an option to enhance its supply capabilities only if it had gone as per the plan.
However, the COVID-19 spread and the lockdowns that followed the pandemic had disrupted this seemingly effortless plan. During the same time, companies have found it necessary to cut down their carbon footprint. Therefore, moving materials from one region to another using fossil fuel-based transportation methods does not seem practical. Similarly, importing materials from China, which has invested heavily in and profited from ores, seems equally problematic.
Even when keeping aside the geopolitical tensions, relying on a single source to get the necessary parts for a potent industry is not the most desirable set-up for many. Therefore, the EU and the US have started using regulations to push the industry towards an unconventional route: prioritising supply over cost.
The Solutions and Issues
The solutions that are being considered by the ore industry are not uncommon. However, they seem to be on the unconventional side of things. Instead of looking at immediate profits and financial stability, the ore supply industry follows a holistic approach. It is imperative that the EV industry needs a constant supply of minerals, especially when consumers are willing to shift to environmental-friendly vehicles. So, instead of waiting for the most cost-effective options — that may ultimately defeat the purpose of a carbon-free future for the industry —, companies must invest substantial capital in many subsectors.
We can find a few examples in the European Union, where the pressure towards reduced carbon footprint is relatively high. Mkango Resources is a popular rare earth developer whose projects are in Malawi. After the long-lasting impact of COVID-19 and increasing demand, the company has partnered with Groupa Azoty Pulawy, a chemical company. Together, they will build a mineral separation plant in the Special Economic Zone of Poland. Similarly, Britain will see one of the larger metal purification centres, thanks to a rare earth developer called Pensana. The developer has its main projects in Angola, but the UK government will assist the company in enhancing the supply chain using the Automotive Transformation Fund. Similarly, companies that localise their ore supply chain tend to receive government aids and tax subsidies.
Nevertheless, shifting the processing centres from Asia-Pacific is easier said than done. While businesses in Asia have retained an efficient framework for the ore supply chain, establishing the same in regions like the European Union or the United States is challenging. Organisations would face many issues, such as the lack of low-cost labour and the presence of stricter regulations. Therefore, a company that relocates its mining and ore-processing infrastructure from China to Europe must be ready for a substantial investment upfront. The same needs to continue for a considerable period, and it becomes a race for survival.
Supply over Cost: The Race for Survival
It is no doubtful matter that the EV industry will need more minerals than ever by 2030. Experts have added that there will be a 637% demand increase for lithium, while cobalt supplies should embrace a 183% rise by the time. However, 2030 is a number that is far away for companies that aim to establish mineral processing units and ore supply chains in Europe and the United States in 2021.
The analytics has not yet predicted the pattern for the increase in demand. However, the optimistic sources believe that companies that can keep the costs minimum will survive the race. However, there is also another narrative that is keeping investors afraid of these movements. Even though the world predicts higher demand for EV-based hardware, price volatility is a concern. Indeed, the price decrease of minerals in the 2017-2020 period compromised many investors' confidence in these ores.
The problem is more common in the case of commodities with relatively small markets. While copper and aluminium tend to get sufficient capital investments, lithium and cobalt are on the verge. The same is the case for platinum and nickel, which hold a relatively better position than lithium and cobalt but are still undermined by aluminium and copper. While it is true that aluminium and copper make up most of the bulk in the EV industry, these vehicles cannot fulfil their purpose without the proper supply of lithium/cobalt.
Market analysts and industry veterans have recommended a few ways to approach the unique scenario. However, we should also keep in mind that companies that start ore processing systems in Europe and elsewhere need to adhere to the changing ESG pressures. Considering these, organisations must take a long-term approach to capital investment with the primary objective of supplying as per the demand. In addition, they must diversify the strategy. It will also be essential to have consortiums that can help them predict and act according to the government policies.
Given the common objective of carbon-free and environment-friendly designs, it is also essential to optimise the EV industry for recycling and reusing resources. Fortunately, government subsidies and tax exemptions can help organisations get the jump-start they want. Yet, despite all these, taking investment-related risks and deriving a comprehensive strategy is necessary for social commitment and pioneering the electric vehicle era that our planet desperately needs.
What the Future Holds
Though we are unsure about the patterns, electric vehicles offer sustenance from an economic and planet-friendly point of view. The ore industry, hitherto monopolised and geopolitically restricted, must be ready for this optimisation, starting with localising the availability of necessary minerals. And putting supply over cost is the only way to avoid a detrimental impact on the EV mobility sector and embrace long-term financial and ethical goals.