Deloitte Flags Barriers to Decarbonising Steel Supply Chain
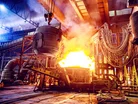
At Deloitte, Ian Sanders serves as both the Global Mining & Metals Sector Leader and as the Australian Energy, Resources & Industrials Industry Leader.
He has more than 30 years’ experience providing audit and advisory services to a wide range of multinational and Australian listed companies across several sectors, including mining, manufacturing, oil & gas and renewables.
“I am passionate about the important role the sector plays in driving the energy transition, and contributing towards a more sustainable future,” he says.
Sanders is co-author of a recent Deloitte report, called ‘Decarbonising the steel value chain: forging new paths together’.
Deloitte report into green steel
The report discusses how the decarbonisation of steel can be accelerated by activating the value chain, and how collaboration plays a critical role in making this happen.
It also identifies some major barriers and proposes potential solutions to overcome these challenges in order to achieve net-zero carbon emissions.
One of the key areas Sanders explores in the report is the decarbonising of steel production, by moving towards green steel technology.
“As one construction company told us, up to 85% of its total emissions are Scope 3 emissions in its supply chain, of which the bulk originates from steel production,” he says.
This, he adds, gives “presents a unique opportunity for the largest steel producers to make a far-reaching impact by decarbonising their operations”.
He continues: “If the 20 largest steel companies decarbonise their plants, the potential total emissions of the steel industry could be reduced by up to 37%.”
This, he explains, would mean moving away from Iron and steel manufacturing via blast furnaces and basic oxygen furnaces, which account for around 95% of the metals’ total greenhouse gas emissions.
He says the remaining proportion of emissions originates from mining (4%) and logistics (1%).
Concentrated Steel production 'presents green opportunities'
The report points out that because global steel production is relatively concentrated, this presents a unique opportunity for the largest steel producers to make a far-reaching impact by decarbonising their operations.
As one construction company stated: “85% of our company’s total emissions are Scope 3 emissions, of which the bulk originates from steel production.”
But steel producers remain reliant on metallurgical coal, as it is an essential fuel for the blast furnaces used in steelmaking, providing both the necessary heat and carbon needed to turn iron ore into steel, and is used to produce about 70% of the world’s 1.8 billion tons of steel each year.
The demand for metallurgical coal is coupled to the demand for steel, and why most primary steelmakers have a division that produces coal for coking, to ensure a stable and low-cost supply.
Steel producers need to move away from coke furnaces
For steel to be greener, producers need to move away from coke-fuelled furnaces and instead use electric-arc furnaces (EAF) fed with steel scrap and reduced iron, and powered by renewable energy, such as hydrogen or electricity.
Sanders says that if steel producers take such action to decarbonise, it will contribute to climate targets of companies across the value chain.
The report states that reducing primary steel production's carbon footprint could reduce emissions by at least 60%.
But Sanders and his colleagues remind us that decarbonising the sector involves overcoming several challenges, the most significant being a lack of affordable green energy supply, underdeveloped environmental policies, and the need for technological innovation to process varying iron ore quality.
Barriers to green steel traction
This report highlights six key barriers to decarbonisation:
- Lack of abundant and affordable green electricity and green hydrogen
- Absence of policy and regulatory incentives to promote global low-carbon steel standards and a fair competitive field
- Limited availability of high-grade iron ore suitable for the direct reduced iron-electric arc furnace decarbonisation route
- Shortage of a skilled workforce to support the decarbonisation transition across the value chain
- Limited capital available to invest in decarbonisation solutions
- Uncertainty of sufficient and long-term demand for low-carbon steel with green premiums
Sanders says: “To enact change, one thing is certain: no one company can decarbonise alone. To successfully decarbonise, core stakeholders in the mining and steel production value chain must work together with end markets such as the automotive and construction industries.
He says there also needs to be “a coalition with partners across the value chain”, including financial institutions and governments, in order to “trigger collective action, spark global and local conversation, drive increased public and private investment, and deliver tangible results”.
________________________
Check out the latest issue of Mining Digital and sign up to our global conference series, Manufacturing LIVE 2024. Mining Digital is a BizClik brand.