Green Steel Push 'Needs New Regulations and Incentives'
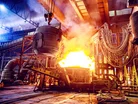
Decarbonising the production of steel is central to achieving global net-zero emission targets, as the steel industry accounts for around 8% of global carbon dioxide emissions and an estimated 30% of all industrial emissions
Paradoxically, steel is also a vital component of the quest for clean energy, being vital for the production of wind turbines and electric vehicles (EVs).
But how difficult, and expensive, is it for producers of steel to make its production more environmentally friendly, and how much progress is being made?
Before addressing these and other questions, first let’s take a quick snapshot of the world steel market.
According to the World Steel Association, global production of steel was 1.88 billion tonnes in 2023, almost exactly the same figure as the previous year.
The largest importers of steel are those countries with burgeoning car industries: the US, Germany and Italy.
The appetite for steel is also being fuelled by the world’s two most populous nations, China and India, both of which are undergoing modern-day industrial revolutions.
Such is China’s need for steel, that it is not only the largest producer of steel – accounting for almost half of the world’s total output – but also one of the largest importers.
Other major steel-producing countries include Japan, India, Russia, South Korea, and the US.
Steelmakers must reduce reliance on coke-coal
One of the problems steel producers have in reducing carbon emissions is their reliance on metallurgical coal. Also known as coking coal, this is an essential fuel for the blast furnaces used in steelmaking, providing both the necessary heat and carbon needed to turn iron ore into steel.
This is why the demand for metallurgical coal is coupled to the demand for steel, and why most primary steelmakers have a division that produces coal for coking, to ensure a stable and low-cost supply.
For steel to be greener, producers need to move away from coke-fuelled furnaces and instead use electric-arc furnaces (EAF) fed with steel scrap and reduced iron, and powered by renewable energy, such as hydrogen or electricity.
Steelmakers are making progress on sustainability. In December 2023, for example, British Steel unveiled a £1.25 billion plan to replace two blast furnaces at its Scunthorpe plant with electric arc furnaces.
Up to 2012, around a quarter of all steel production was from EAFs, but the migration away from fossil fuels has accelerated since then. In 2017, EAF steelmaking production hit a new high, with a 7.5% year-on-year increase – followed by a 12.3% increase in 2018.
A new report from Global Energy Monitor (GEM) shows that last year, 43% of steelmaking capacity was based on EAF technology.
Green steel needs regulations to hit next level
But the reality is that steelmaking is unlikely to make further significant reductions in its reliance on coke without both a change in regulations and also price incentives, to drive a shift in steel investment and consumption.
The price premium on green steel is around $150 a metric ton, according to the consensus of presentations at last week’s Global Iron Ore and Steel Forecast Conference, held in Perth in Western Australia, the state that produces the bulk of the world’s exported iron ore.
Reuters reports that even a relatively modest premium on green steel makes it unattractive to much of the market, with automotive manufacturing being the only sector prepared to pay a premium for green steel, because it is able to absorb the extra cost into the retail price of a vehicle – and also gain significant consumer kudos for making an environmentally friendly product.
However, Reuters points out that the biggest steel consumers are property and infrastructure, which used a combined 518 million tons in 2024, or 57% of the total. It also points out that high-speed rail uses between 30,000 and 60,000 tons of steel per kilometre. Higher-price green steel remains unattractive to these sectors.
This is why, it says, that sustainability regulations around steel production are needed to take decarbonisation efforts to the next level, coupled with fiscal measures such as carbon border taxes.
- IEF on 'Paradox' of Mining's Role in Quest for Clean EnergySustainability
- Deloitte Flags Barriers to Decarbonising Steel Supply ChainSustainability
- Steel Recycling 'can Counter Coal & Iron Mining Carbon Cost'Sustainability
- Conflict Minerals: Navigating Ethical Sourcing ChallengesSourcing & Procurement