Westmoreland Coal: Progressing into the Future
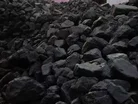
Westmoreland isn’t your ordinary coal company. Through progressive practices and a unique business model, the 159-year old company is adapting for the future, and in doing so, helping modernize the coal mining industry for the better.
Founded in 1854, Westmoreland Coal is one of the oldest mining companies in the United States. Having predominately been an underground coal production company, Westmoreland transitioned over to a mine-mouth operation in 2001 with a greater emphasis on customer relationships. This allowed the Company to be the lowest-cost fuel supplier to some of the most utilized coal utility-owned power plants in the United States.
“We do have a bit of a different business model, but it has allowed us to be successful when others have not,” says Bob King, CEO and President of Westmoreland Coal. “We’re looking to grow and locate opportunities to add value to our company.”
Although Westmoreland has adopted a new business model, the Company isn’t changing its values. Company culture and employee safety still plays a central role for Westmoreland but now more than ever the company is striving to continuously improve those values. In addition, Westmoreland is implementing new technology and equipment to improve the efficiency and reclamation process in the coal mining industry.
Utilizing more technology
Now more than ever technology is playing a vital role in coal mining. With the creation of GPS and advanced software programs and mining equipment, the coal mining industry is finally coming of age.
“The mining industry has come a long way because of technology over the last 20 years,” says King. “GPS is one of the major technologies we use in our operations. Advanced equipment has helped as well. At some of our mines we have systems that can track our equipment; it will identify mechanical or maintenance issues and record it electronically.”
Utilizing more technology allows Westmoreland to maximize the most of its resources.
“We’re going more and more to direct links from equipment to data capture, which is playing a significant role in helping with preventive maintenance,” says Tom Durham, VP of Planning & Engineering. “GPS technology helps to assist in blast design and hole location. The unit on the drill actually logs the hole so we know exactly how to load it to get the most efficient use of explosives with the least amount of vibration from the blast. We also use GPS technology on tractors for grade control in reclamation. Use of the technology improves productivity and therefore reduces costs for our customer.”
The Company is also implementing more technology into its day-to-day business operations. It has initiated an enterprise wide platform for reporting and analytics, as well as analyzing data it accumulates from its equipment.
“Computer programs allow us to take this data and analyze it, helping us make decisions on where we should focus our activities and what areas need the most improvements,” says King. “We are definitely using and incorporating technology into all of the aspects of our business.”
Westmoreland is currently migrating all of its servers to a virtual environment on a single platform allowing the company flexibility to grow and expand. Automation is another key factor the mining company is looking into.
“We’re looking at IT to improve our revenue system, assist in tracking of coal shipments, customer information and quality. We’re looking at global solutions to automate time and labor processes, says King.”
Employee and Company Culture
Westmoreland has about 1,400 employees at its six mining locations, including its corporate office in Denver, Colo. Through the years the Company has instilled a strong company culture of treating employees right through its cornerstones.
According to King, “We have a set of values that is embedded in this company with safety being number one. It’s a value not a priority because priorities change, values don’t. We also value continuous improvements. If you’re going to be competitive in this industry you have to continue to grow as a company and continue to take advantage of all the latest technology to improve. The environment is another one of our values as we want to be good neighbors to our communities. Mining is a disruptive activity but the intent is to use that land and then get it into the same shape, or better, once you’re finished. So it’s a sustainable business practice that allows our neighbors to see we’re responsible.
In addition to winning numerous awards for environmental practices, novel practices and sustainable practices, Westmoreland has won several safety awards, including Sentinels of Safety, as well as setting safety records. According to King, “Those are the kind of things people recognize when they come to our company and they’re proud to be a part of that experience.”
To recruit new employees the Company visits college campuses and trade schools for professional and skilled workers. These schools include Montana Tech, Colorado school of Mines, Missouri University of Science and Technology, and Virginia Tech.
“The college campuses we recruit on are what we consider the leading engineering schools in the country,” says King. “We’ve had considerable success recruiting interns as well as retaining our selection for full-time employment.”
Improving for the future
Like any great company, Westmoreland is continuously working to improve its business. Far and wide the largest improvement the company is always working on is safety. It’s an ever-changing practice to stay ahead of the industry and collaborate with companies to keep employee safe.
“The industry is very collaborative in regards to safety,” says King. “We take part in industry activities such as mine rescue programs and we’re very active in making sure all of our sites have mine rescuing and emergency response abilities. We’re involved in the Rocky Mountain Coal Mining Institute and some of our employees are leaders in the organization in regards to organizing safety and emergency training efforts.”
The Rocky Mountain Coal Mining Institute (RMCMI) representing the eight western coal producing states is an organization founded for education. The corporation holds annual meetings with educational programs pertaining to coal mining technologies, production techniques, mining management, safety, state and local laws, and other energy related issues. Each year the institute holds simulated mine rescue evaluations with 8-12 teams participating from other states. “We specifically set these evaluations up so the teams work together, communicate and learn from each other,” says Durham.
By continuing to improve upon its company culture, safety initiatives and utilizing the latest technology, Westmoreland is looking to adapt its business for the future.
- Huawei: Huaneng Ruichi's Autonomous Electric Mining FleetSmart Mining
- South Africa Mining Sector Holds Breath on NationalisationSupply Chain & Operations
- Brightstar, Eldridge and Claure acquire AusencoSupply Chain & Operations
- First Quantum contracts with MECS to cut emissionsSupply Chain & Operations