The benefits of the Caterpillar R1700K underground loader
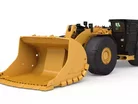
Minexpo 2016 – remember that?
I’m sure most of you do, especially if you’re interested in the latest underground mining vehicle technology.
Well, Cat® announced just that – the new R1700K Underground Loader, featuring multiple engine configurations, a new ergonomic operator cabin and greater payload to help miners drive down costs and boost productivity.
In this modern market, productivity (which we reported to be down across the industry) and cost efficiency is crucial.
“The R1700K Underground Loader is designed to help customers lower cost per ton—through increased payload, improved pile penetration and greater breakout forces,” said Steve Rich, Product Manager Hard Rock Vehicles for Caterpillar.
The R1700K will be put through the paces, with rigorous field testing in 2017 before commercially launching in 2018.
So let’s take a look at what makes the R1700K Underground Loader one to keep an eye on:
First things first, straight from Cat: “The compact profile, efficient power train and rugged construction deliver low cost-per-ton truck loading and load-haul-dump production in underground mining applications”
Cat promises that the loader delivers a payload of 15 tonnes (16.5 tons), which is an impressive 20 percent more than the previous model and supporting efficient three-pass loading of the 45-tonne-capacity (50-ton-capacity) Cat AD45B Underground Truck
Multipole engine configurations are available for the Loader in a bid to enable miners to better optimize the loader for lowest total costs in various applications. So, all configurations use the proven Cat C13 ACERT™ engine. This engine can be configured for applications that require compliance with the highest emission standards in underground applications. Not only that, the engine allows optimisation for customers who are striving to improve underground air quality.
A mining operation is only as good as the miners themselves, which means safety is paramount to efficiency.
An open ROPS/FOPS cab and an enclosed cabin will allow increased leg room, multiple ergonomic adjustments, and automatic climate control and filtered ventilation in the enclosed cab enable operators to work in a comfortable environment.
Underground mining is not without its complications and the need for simplicity can make a huge difference in productivity. In comes the Loader.
Pilot hydraulic controls enable precise operation with low effort. Switches and control panels are located central to the operator and within arm’s reach for fast adjustment to the operation of the machine or systems. There is even an optional rearview camera that can display its view on the easy-to-read color LCD monitor.
It doesn’t stop there, the LCD monitor presents live diagnostic code feedback- meaning users are able to identify an issue effective immediately and work to fix it as quickly as its noticed.
Moving more, safely
The bucket has an increased throat angle to allow for faster filling and better material retention during tramming. New Cat Bolt On GET (Ground Engaging Tools) are designed for use in abrasive applications where high wear rates make welded GET impractical.
The system also delivers more available wear material for longer life and greater uptime. Built-in wear indicators and replacement corner segments allow the system to be integrated into scheduled maintenance regimens.
A traction control system enables complete control over drive power to each wheel independently. This means minimal tire slip, optimum traction, and the ability to penetrate the pile more effectively for fast loading.
It is equipped with multiple subsystems for fast technology implementation. The Cat line-of-sight remote control systems allow operators to control their machines from safe distances, and the Cat Command for underground, semi-autonomous system enables operators to work from a remote location. Remote machine health monitoring, payload monitoring and other technology options can be installed at the factory or in the field.
The October issue of Mining Global Magazine is live!
Follow @MiningGlobal
Get in touch with our editor Dale Benton at [email protected]