Mining with data: How technology is disrupting the sector
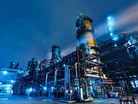
Big data analysis is an invaluable tool with many companies from finance, logistics and tech harnessing the power of the ’new oil’. Even construction is now finding a way of feeding its bottom line from big data analysis – the act of deciphering data to predict and forecast new items and trends.
Now, big data is being used by scientists to predict the location of new, so-far-unknown minerals and by doing so, is reshaping the entire mining landscape…
Big data in practice
Along with a team of scientists, Dr Shaunna Morrison from the Carnegie Institution for Science in Washington D.C. is working with the US Geological Survey to unearth new mineral deposits. Using big data network analysis, they are assessing what minerals are already in existence and making predictions to discover what else might be out there, and their work has proven very successful - just a couple of weeks ago they found a new type of cobalt.
READ THE LATEST MINING GLOBAL MAGAZINE
Large organisations such as Amazon and Netflix apply big data to their market basket analysis to predict consumer habits and now mining companies could be doing the same. “Looking at the spending profiles of customers is very similar to looking at the formational patterns of minerals,” Morrison says. “These practices are being implemented across the board by all these huge companies. They're very powerful statistics."
A groundbreaking paper published in the American Mineralogist reports the first application to mineralogy of network theory, which is best known for analysis of e.g. the spread of disease, terrorist networks, or social media.
Many believe that the results could pioneer a way to reveal mineral diversity, evolution and distribution worldwide. “The quest for new mineral deposits is incessant, but until recently mineral discovery has been more a matter of luck than scientific prediction,” says Morrison. "All that may change thanks to big data."
To reap the benefits of big data, organisations need to be cognizant of economic geology. "Without doing these statistics they’re relying on their knowledge and experience,” Morrison explains. “They’re very familiar with how copper deposits form and the specific environments they form in. They have to be aware of where that environment is, anywhere on the planet. Sometimes that’s not obvious if geological mapping hasn’t been done somewhere. If a huge copper deposit hasn’t been found, it's very likely it's because it hasn't been mapped."
Data challenge
This tool generates a tremendous amount of data and creates an issue in terms of accessing quality information, according to Morrison. “There's tonnes of information out there but how do you get that out? And how do you get that in a form that is machine-readable? It's a huge undertaking. The mineral evolution database, which is what we use for most of our studies, has been assembled over a period of eight years by an army of undergraduates putting this together at the University of Arizona. So, one of the biggest challenges is certainly acquiring that data.”
The network analysis technique enables scientists to represent data from multiple variables on thousands of minerals, sampled from a multitude of locations within a single graph. These visualisations can reveal new and unique patterns of occurrence and distribution and patterns of mineral coexistence. Scientists can then see which geological, physical, chemical and biological characteristics are necessary for the mineral appearance. It is then possible to predict what minerals might be missing, as well as where to go to find new sources.
Big data is also helping the physical processes of mining too. Jason Knuth, Product Manager of Analytics & JoySmart Solutions at construction and mining group Komatsu, explains: “Every machine is unique in terms of the challenges they face. This includes tough operating conditions and variety of materials. It’s why we collect so much data off of our machines.
"In order to accurately predict machine behaviour, you have to understand what normal looks like. You have to build customised models that are unique to each machine and the conditions they’re in. Then as the conditions change, so do the models and predictions,” he says.
"We focus on looking at abnormalities in the data from typical operations and highlight abnormal behaviours. You can’t prevent what you haven’t seen. But the more data we have and the more data we process, the more we understand and the more we can help prevent issues for our customers.”
For Komatsu, this sheer quantity of data is a good thing. “For our engineers and data scientists, there’s never enough data,” Knuth says. “More data means more visibility, more clarity, increased modelling, and increased information. All of that leads to better response times for our customers and a better understanding of equipment needs for future development.
“Data storage is expensive and that can be a concern of course,” he adds, “but Komatsu has a data management strategy that allows us to archive the information at a lower cost, prioritising the most relevant and recent information while still allowing access to archived data.
"Because we are the original equipment manufacturer, we can do increasingly more computing and analytics on our own equipment, and less in the cloud. Getting that computing power closer to the machines helps with data storage and speeds up the flow of information and processing. Ultimately, that is our focus, turning the raw data into useful information and actionable items, and getting that into the right person’s hands in time to improve processes and prevent issues.”
Big data in the future
Over the next couple of decades, Knuth envisages machines will become more intelligent, which will tie in with Komatsu's growth. “Machines are going to continue getting smarter with more onboard computing,” he says. “At the same time, automation will continue to advance, allowing for the increased use of remote operation.
"As we continue to grow and improve our ability to turn raw data into information and results, that will be the glue that helps bring together various autonomous projects and capabilities on a mine site, enabling coordinated remote operation and monitoring. This will help keep more people from harm’s way while optimising machine performance and mine coordination, to enhance safety and production capabilities.”
Morrison believes the advancement of data analytics will enable mining companies to become more aware of where the earth's resources are, and differentiate between the minerals they need vet against the worthless gangue minerals they don’t.
“This will save them a lot of time, and therefore a lot of money in trying to find them,” she says. “If they're better able to characterise the minerals, that dramatically determines the economic value and viability of getting them out of the ground.”
“We’re on the cusp of a huge change in mineralogy and mineral resources, and in the understanding the mineralogical makeup of our planet,” Morrison adds. “In the next 10 years, we're going to see an explosion in this type of work.”