What You Need to Know When Considering Automation in Drill and Blast
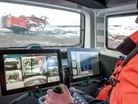
The use of automation for drill and blast is fast becoming an area of great focus for mining companies who are looking for ways to significantly improve productivity and increase profit margins. But many organizations often underestimate the automation journey and the requirements needed to successfully optimize drill and blast operations.
• How-To: Optimize Drilling and Blast Effectiveness
• World's largest mining blast ever recorded
Mining IQ caught up with Gary Cavanough, Principle Research Scientist at the CSIRO, to discuss specific examples and trends of automation in drill and blast and how they’re influencing both efficiency and operational expenditure.
Some of the biggest challenges facing drill and blast teams are hole positioning, diameter accuracy and hole dipping. How is automation able to mitigate these risks?
If you take open cut coal mining as an example, drilling and blasting accounts for approximately 10 to 15 percent of mining costs. Outcomes in drill and blasting operations can significant affect the cost of other operations, such as a blast with poor fragmentation and lead to an extra $300,000 or even $400,000 cost to digging.
In relation to hole positioning and hole dipping, current practice is to print out a list of hole numbers and a map of their position. This is taken to the bench, where each hole must be located manually, measured with a tape measure and the hole depth written onto the print-out list.
At the end of the shift, this is taken back to the blast designer, who then manually enters this data into the blast design software to generate loading sheets. The automatic hole dipping system is uploaded with drill hole numbers and GPS coordinates of each hole via Wi-Fi from the blast design software.
On the bench, the hole is identified and measured, with information transmitted to the blast design engineer; real time data comprising the actual hole position, depth, and depth of water, which might be in the blast hole. The blast hole load sheets are then generated using this information.
Diameter accuracy is important because if you have a planned 229mm, which is in fact 240mm (due to bad drilling of the ground), you’ll need to load 10 percent more explosives – mines generally know regions where this occurs.
‘On drill’ scanning systems need to be developed to accurately measure blast hole volumes. This could be a data mulling system, whereby the instrument scans a hole as the drill is withdrawn from it and the data is transmitted when the device reaches the surface.
A major development would be to monitor blast holes prior to, at and after loading. Prior to loading, there is real time monitoring of hole depth, temperature and the depth of water (should it be present).
At loading, there is a real time measurement of the depth of explosive column; whilst after loading, there’s real time monitoring of the temperature and density of explosive products.
After the holes are drilled, a low cost sensor cable is placed in each hole, and the cable is prewired to a wireless transmitter. Before the hole is loaded with explosives, the sensor cable monitors the depth (cave-in detection), depth of any water present, and hole temperature.
This information is used to plan the blast hole loading and identify hot holes. During loading, the sensor cable monitors depth of the explosive column as the explosive fills the hole.
After the holes are loaded with explosive products, the same sensor cable is used to monitor density and temperature of the products. Subsequent data can be used to:
• Monitor the holes during sleep time, and ensure that the density is not approaching a critical value
• Detect any water ingress of explosive products (due to a decrease in density and temperature)
• Identify any reactive ground reactions (due to a significant temperature increase). At detonation the same sensor cable is used to measure the Velocity of Detonation.
What are other examples of innovative automation trends that you’re seeing?
Underground: Top hole hammers have limited depth due to energy loss caused by drill couplings, as well as accuracy issues. An exciting innovation are down-hole hammers to enable drilling of longer, more accurate holes for massive blasts, which are traditionally conducted with air hammers.
Water hammers have had limited use due to requirements for high pressure clean water. However, water recycling or cleaning units are now becoming available to make water hammers more viable.
They are able to drill much more accurately than air hammers due to the small aperture between the drill rods/motor and the wall of the hole. Teams can subsequently drill longer holes without the risk of over-sized rocks remaining after blasting (over-sized rocks are a big problem in underground mining as they are very difficult to handle).
Water hammers should also produce smoother holes to ensure packers seal the hole for fracking, which is used to pre-condition for block cave mining. There is significant automation in these long hole water hammers, including steering and survey.
Fiber optic survey systems are in development to allow fast, accurate survey of underground blast holes. These are in the form of a fiber embedded in a flexible ‘snake’ which pushes into the borehole, and the shape of the fiber is then measured. It has previously been a tedious operation to survey holes upwardly. Accurate hole survey will allow the most effective blast design and remediation prior to blasting, should the hole trajectories indicate a poor blasting outcome.
Open cut:
1. Remote control drill rigs have been developed and used in Australia. A company in the USA offers a service to retro-fit out the drill rigs for remote operation.
2. Pick type drill bits are now available. This requires less pull down force than conventional Tricone bits and higher air flow rates to carry out larger particles. Pick bits offer the opportunity to increase drilling rates but require rigs to be modified.
Additionally, for bulk mining operations, the development of bulk explosives trucks (MMU) will enable faster explosives production and delivery. Current practice for wet holes is to pump explosives into the blast holes by placing a hose at the bottom of the hole and raising it as the hole fills with explosive (displacing the water). This is very slow when you’re charging hundreds of deep holes.