McKinsey: firms must invest in Remote Operating Centers
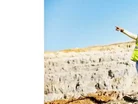
It's been a year for remote working with the COVID-19 pandemic - and the mining industry is not exempt from the changes.
Some firms have started to relocate around 15–20 percent of their on-site workforce by setting up “control towers” to facilitate remote working, according to McKinsey's Remote Operating Centers in mining: Unlocking their full potential report, which is helping the industry develop more resilient, responsive, and flexible operating models suited to an increasingly uncertain environment.
Yet more needs to be done. McKinsey's research unearthed a common theme underpinning the root causes for failure; insufficient emphasis on and investment in developing a robust change-management strategy and subsequent implementation.
It lays the responsibility for change with leaders, who do not set clear expectations of bottom-line impact from ROCs and/or position the ROC with limited authority within the organization.
Drilling down into the Remote Operating Center (ROC) landscape, it discovers:
- Some companies have implemented cloud-based systems that aggregate site data into a single data lake that can be accessed, analyzed, and visualized for decision support, creating a “room of screens”.
- Other companies manage and actively control plant automation systems, fleet management systems, and remote-controlled machines from the ROC.
- The most sophisticated companies manage all these functions on a larger geographic scale, covering the value chain from end to end, optimizing post-processed ore logistics and port facilities used by multiple mine sites within a region, with regional parts and supply warehouses monitored across multiple assets for supply-chain optimization.
- The larger span of control of such operations helps to maximize best-practice benefits across site assets to drive operational improvements such as predictive maintenance among similar mine fleets.
Companies usually focused on a combination of four value levers when implementing ROCs:
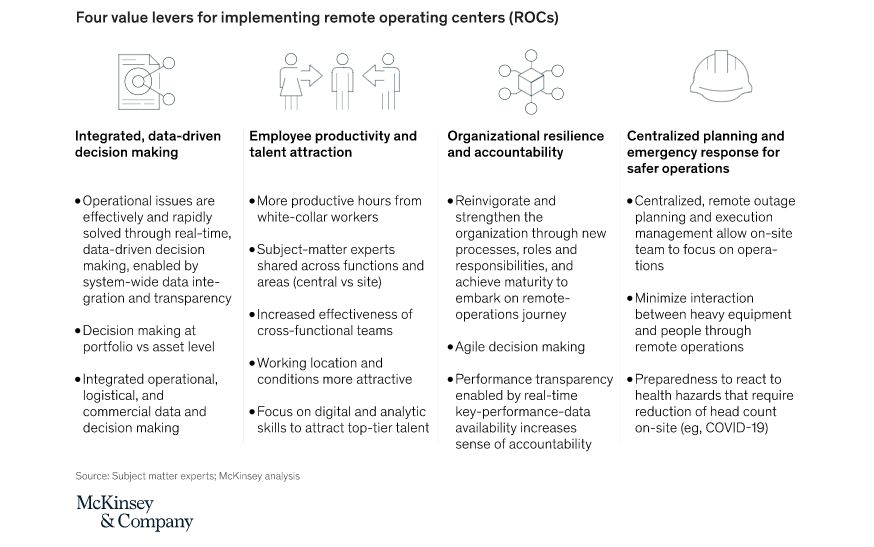
It advises companies to embrace five key principles when creating value out of ROCs:
- Define a clear and compelling business case around the value creation for the organization
- Take a robust approach to organizational integration and change management
- Ensure the organization is set up to attract and nurture the best industry talent to drive long-term performance and growth
- Create the technology backbone of the ROC through technology stack and facilities integration
- Understand social, environmental, and legal impacts