Case study: Partnering for improved machine reliability
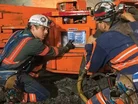
This is a case study by Joy Global
A mining customer’s maintenance strategies were producing good availability results, but to achieve consistency, the customer wanted better visibility on potential upcoming causes of downtime. In this tough environment, major component failure events need to be controlled to minimize impact against budget, and an enhanced solution was required to improve margins.
Solution Design: Joy Global approached an existing customer about engaging in a trial period where the two would partner through the company’s JoySmart Solutions offering to improve machine reliability and avoid catastrophic failures on major components. The customer agreed to give Joy Global six months to prove the value of the offering at its coal mine in Australia.
The JoySmart team proposed implementation of a newly-developed automated monitoring system that trawls through machine data with the ability to detect any changes in component behavior to predict an onset of failure.
• Related: [VIDEO] Joy Global and the Internet of Things
“The key for us was to create an algorithm that was sensitive enough to pick up small changes in component indicators while not creating unnecessary alarms,” said Trevor Griffiths, product performance manager with Joy Global.
The strategy was to build on the existing partnership by employing new technologies and concepts to reach the next level of performance needed in today’s mining industry.
Implementation needed to be quick and effective, with a six month “proof of concept” plan to determine whether the new approach would continue.
The Solution: JoySmart product specialists quickly identified areas of focus that would be prioritized to achieve improved reliability:
• Major Equipment: motors, transmissions, gearing, bearings
• Lubrication
• Air Supply
Major equipment monitoring provided the necessary risk management element, whilst air supply and lubrication were identified as systems that had the most impact on reliability.
An engagement strategy was discussed and implemented that had clear lines of communication and accountability. Both companies understood that this needed to be a partnership with common goals and a unified approach.
Using collected sensor data, JoySmart Solutions experts deployed predictive models that could analyze real time sensor data to determine if any of the identified major equipment or systems was starting to drift from “normal” operation. On a daily basis, JoySmart product specialists would intercept any model detections and then report out with a recommended course of action, giving it a priority rating depending on the component type and severity of the detection.
• Related: [INFOGRAPHIC] The 2016 Mineral Exploration Roundup
With a system in place, the necessary change in culture was the final hurdle. In the first two months of implementation, a situation arose where an imminent failure condition was detected and reported, but not all recommended steps were followed, resulting in 38 hours of downtime that could have been avoided. Following that incident, team engagement and commitment rose, allowing greater successes to be achieved through the partnership.
The Results: Toward the end of the six-month trial period, the combined machine availabilities hit target eight weeks in a row.
One of the main drivers of change, the need for consistency in machine availability, was now being achieved.
No major equipment failed during the six-month period. The benefits of the partnership were so clear that a planned review of the trial period was deemed unnecessary, and the customer decided to proceed with a long-term partnership. Working together with the JoySmart Solutions team, the customer continues to improve performance every week through new ideas and strategies developed.
Stay connected! Follow us on Twitter and like us on Facebook
Featured Articles
A fleet of Huaneng Ruichi autonomous electric mining trucks have been deployed in China, supported by Huawei's Cloud Services and 5G-Advanced network
Rio Tinto completed its US$6.7bn acquisition of Arcadium Lithium, making it a key company in raw materials mining for batteries in the energy transition
Intel first began to work towards responsibly sourced conflict minerals from the Democratic Republic of Congo and adjoining countries about 12 years