Hydropower Taking Over Compressed Air Within Drilling Applications
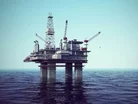
Corporations and groups throughout the mining industry continue to dig deeper into innovations that could potentially improve efficiency and cost-effectiveness of their drilling operations. It is also the hopes of these mining corporations and groups that these improvements and new innovations could also help them to not only weather fluctuations regarding decreased demand in some markets, but, hopefully, help them to keep pace with growing demand in others.
Among the top factors that have continuously slowed mining companies and mining technology groups from not just developing these mining drilling operations, but actually bringing them to market for actual mining applications is safety. Mining operations pose extreme working condition and require an immense degree of dependable and stringent safety standards that must be upheld.
This is one reason why compressed air has been a very important source of power in virtually every type of mine for many years now. Compressed air continues to be applied to drilling in the mining sector as a source of power for drilling holes for blasting in underground mining. Not only that, but compressed air has also remained a go-to source of power for its flexible use with a variety of other applications both inside and outside the mines. For example, mucking machines, scraper-hoists and ventilation fans represent a few of the areas of application that take advantage of compressed air.
Up until recent history, compressed air has not just been the most popular choice for powering drilling and other applications throughout the mining industry, it has also been viewed as virtually the only true option. However, recent developments in mining technology now point to hydropower equipment as a much stronger, potentially viable alternative to compressed air. While hydropower in and of itself has been around for a significant amount of time, innovations regarding its application throughout the mining industry present some undeniable benefits well worth looking into for both small and large mining corporations.
“The biggest combined force driving the adoption of hydropower equipment in the underground mining industry – specifically in gold and platinum mines – is the need to move away from using compressed air and an understanding by industry that it must do so,” says hydropower specialist Hydro Power Equipment (HPE) Innovation Manager Peter Fraser.
When compared to using compressed air in mining operations, Fraser points out a few key, unique advantages that the use of hydropower can deliver. “Hydropower equipment is energy efficient because of the intrinsic efficiency of the positive displacement of water hydraulics and the absence of leaks. It also has lower operating costs, as localized hydropower systems feeding a local network of small bore pipes on a half-level stope are noted as the lowest cost method to power all the operations required for conventional mining,” Fraser says. “Hydropower drilling has higher penetration rates than compressed air drilling, which allows for a quicker task and, subsequently, a reduction in the risk of a lost blast and of unnecessary exposure time of drill operators on the face. Compliance with noise and other environ-mental requirements is yet another driving factor behind the adoption of hydropower in the platinum and gold mining industry,” he adds.
Fraser goes on to explain that hydropowered drilling rigs have achieved mainstream acceptance in man-free box-hole development and in flat-end development and hydro stoping, which uses either centralized or localized hydro systems. Other applications for hydropower in underground platinum mines include the establishment of hydropowered box-hole chutes, roof bolting and stope cleaning. What’s helping spread the application of hydropower is that small and large mining operations alike can take advantage, leaving behind the inefficiencies of compressed air. “For example, a new section in the mine could be developed as a stand-alone localized hydropower operation, while the compressed-air operation can be maintained for the existing operation,” Fraser says.
Recent, innovative developments of hydropower include more accurate and truer drilling. Among the many benefits offered by this is the quicker and safer development of box holes. Reef boring and long-hole stoping mining methods and equipment have seen significant improvements from hydropower applications as well. These developments have also led to less dilution of ore while improving the safety of miners having to enter stopes.
With immense benefits such as long straight holes, low energy consumption, and an oil-mist and dust-free working environment, we can likely expect a continued rise in the application of hydropower drilling throughout the mining industry.
- Cornish Lithium starts second drilling at TrelavourSupply Chain & Operations
- Sandvik DL2711 & DL2721 | Sandvik Mining and Rock TechnologySupply Chain & Operations
- High tech mining technology used to help drought-stricken farmers find valuable waterSupply Chain & Operations
- OceanaGold’s Haile drill and blast team gets remote techTechnology
Featured Articles
Rio Tinto completed its US$6.7bn acquisition of Arcadium Lithium, making it a key company in raw materials mining for batteries in the energy transition
Intel first began to work towards responsibly sourced conflict minerals from the Democratic Republic of Congo and adjoining countries about 12 years
International Energy Forum says mining is the 'paradox' at heart of quest for clean energy but recognises the industry is addressing sustainability issues