Is shovel-based payload monitoring more productive than truck-based methods?
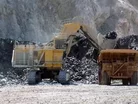
Global mining technology provider MineWare believes shovel-based payload monitoring is set to supersede traditional truck-based methods through the delivery of significant cost savings, more accurate data and ultimately, more consistent payloads in trucks.
MineWare founder and CEO Andrew Jessett claims variations in operator performance and material properties remain a significant and costly issue for the mining industry globally.
“Payload is essentially the load carried by a piece of equipment—in this instance, in the bucket of a shovel which is then dumped into the truck,” explained Jessett.
“The key to improving shovel productivity and reliability is to provide timely, accurate and clear data to all stakeholders in the shovel operation, ultimately resulting in more consistent loading practices. Shovel based payload systems can achieve this goal.
“Traditional truck-based payload methods have inherent challenges such as truck sensor calibration, trucks lacking a weighing system altogether, and the length of time it takes for payload data to reach the operator. These challenges can impact on the accuracy of the information and the usefulness of the data. Keeping a fleet of truck payload systems accurately calibrated is a challenge for any mine site,” he said.
• Related content: [INFOGRAPHIC] Cost comparison: Hardrock exploration v.s. lithium brine
Jessett claims that the lack of a consistent truck loading control system can result in a number of costly impacts such as truck overloads, truck underloads, at-face dumping, and truck bunching (where heavily loaded trucks become slower up-ramps holding up other trucks and creating bottlenecks in production).
“All of these impacts can lead to lower production rates and higher haul truck maintenance costs, including premature tire failure and higher fuel costs,” said Jessett.
“By providing real-time feedback to the operator, shovel-based payload monitoring systems enable well-trained shovel and excavator operators to consistently fill the trucks with a smaller variation in the final truck load.
“If truck payload is more consistent, productivity will improve and operating costs reduce.”
Referring to a recent case study with one of MineWare’s North American mining clients, Jessett highlights that Argus was responsible for achieving an increase of more 10% in truck loading performance.
“For our client, that meant an average increase of 39 tons per load, per truck. And based on 14,000 loads, that’s 546,000 more tons every month and a hefty financial gain of more than $1million per month—based on $2/load.”
According to Jessett, MineWare’s Argus Shovel Performance Solution is one of the only systems on the market that provides accurate ‘shovel based’ payload management for controlling truck loading.
“It’s really important to have trucks loaded to their target weight. With Argus, we’re able to ensure that the operator knows how much is loaded in each truck and, in real-time, how much remains to be loaded. Having this information to hand enables the operator to achieve more consistent loading,” he said.
Jessett emphasizes that even a one percent production improvement on large machinery like draglines, excavators and shovels can deliver significant outcomes for mine sites.
“In the field, we’re seeing significant performance improvements by using Argus loader-based payload management to move more for less and without overstressing the equipment—therefore reducing unit costs,” he said.
• Related content: [VIDEO] Improving fleet management with Caterpillar's MineStar technology
“Many of our clients’ operations are doing anything from seven million tons to 100 tons per annum.
“For them, getting accurate and reliable payload information, and being able to achieve consistency across operators in regards to their performance are key to productivity improvement,” he said.
“In their words, ‘if you can measure it, you can manage it.”
About MineWare
MineWare is a global leader in the development of advanced dragline and shovel monitoring technologies for the global surface mining industry. Since creating the industry's first fully integrated dragline monitor in 2005, MineWare has continued to advance its core technologies including the Pegasys dragline monitor, Argus shovel performance system and remote monitoring and data visualization tool mRoc Desktop. Today, MineWare is improving the performance and productivity of more than 120 draglines and shovels around the globe with a team of more than 50 staff operating throughout our offices in Australia, South Africa and the Americas.
Stay connected! Follow us on Twitter and like us on Facebook
Featured Articles
A fleet of Huaneng Ruichi autonomous electric mining trucks have been deployed in China, supported by Huawei's Cloud Services and 5G-Advanced network
Rio Tinto completed its US$6.7bn acquisition of Arcadium Lithium, making it a key company in raw materials mining for batteries in the energy transition
Intel first began to work towards responsibly sourced conflict minerals from the Democratic Republic of Congo and adjoining countries about 12 years