Worley: Tech Key for Copper Ramp-up to be Sustainable
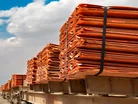
Claudio Martinez is VP, Global Copper Sector Lead at Worley, an Australian engineering professional services company servicing the resources and energy sectors.
Why is copper so in demand?
As a critical energy transition metal, a dramatic increase in copper production will be fundamental to the global rollout of clean energy. Delivering the energy transition will require a near doubling of copper production over the next decade and by 2050 demand is forecast to exceed all the copper ever consumed worldwide between 1900 and 2021.
Surging demand for copper could create a significant supply shortage by 2031 and shortfalls could drive copper price rises of 20-50%.
What challenges does the copper industry face?
Copper grades continue to fall and many remaining ores are harder to process, resulting in greater quantities of material being processed. This uses more energy and water, and creates more tailings – all just to achieve the same copper output.
Copper mining now uses the equivalent of 10 times the amount of water in Sydney Harbour, and the copper industry produces 0.2% of the world’s carbon footprint each year across Scopes 1, 2 and 3 emissions.
And, while demand is increasing, supplies are drying up. Many of the most copper-rich regions are experiencing severe droughts, worsened by the effects of climate change. The industry clearly needs to find a more efficient and sustainable path to scaling up supply.
Is technology helping with copper production?
There is a range of promising new technologies for sorting, grinding, flotation, leaching and filtering that could allow more efficient, economical, and sustainable copper production.
For example, some grinding technologies or coarse particle flotation or filtering can simultaneously improve recovery while minimising the need for energy-intensive grinding, reducing water consumption and tailings costs.
To date, few mining companies have assembled these technologies together, and many are yet to be deployed in copper mines. Engineering and delivery expertise will be essential to bridge the gap between laboratory development and real-world deployment so that these innovations can be properly demonstrated in the field and carefully configured to real-world conditions.
Are there barriers to tech adopting in copper mining?
The copper industry remains conservative, with many processes still using century-old technology. New innovations are often introduced incrementally and in silos focused on improving specific aspects of production, instead of a more radical approach of a clean sheet review of the entire process.
This traditional siloed approach is exemplified by the historic separation between copper mining, water operations, power supply and land usage, even though all need to be collaboratively managed.
What is the key to innovation in the copper industry?
Taking an ecosystem approach. Unlocking the potential of new innovations requires a holistic technology-neutral approach harnessing everything from water operations to new processing technologies to drive economic and environmental efficiencies across the flowsheet.
For example, mining companies could combine dry storage systems that save water, by adopting water desalination plants to reduce water consumption and create more secure and sustainable water sources. Such a comprehensive, end-to-end approach uses the full mix of mining innovations, and can optimise every stage of production and produce greater environmental improvements.
What role is Worley playing in tech adoption?
Worley is involved in supporting technology providers to enable real-world deployment of vertical roller mills. These systems could replace the current two-stage milling process with a single machine that consolidates the entire end-to-end milling process to produce a product suitable for downstream processing.
This can be done without using any water and can reduce energy consumption by over 30%. A ‘copper sponge’ material, developed by a technology provider to the minerals processing industry, is highly selective and reusable. This eliminates froth flotation, reduces water consumption and the need for added organic reagents while improving the concentrate grades early in the process.
We are contributing to an initiative aimed at enhancing the deployment of copper sponge technology at an Australian copper mine. Such technologies can be integrated and tailored to generate similar benefits across the entire spectrum of copper production, from extraction to the creation of the final product.
Can increased copper production be sustainable?
To increase copper production at the required pace and within environmental limits, the industry will need to adopt and deploy sustainable new mining innovations at a greater speed and scale than ever before.
Engineering expertise will be crucial to rapidly translate and tailor new innovations for a range of real-world conditions. The key will be to adopt an ecosystem approach applying new innovations cohesively across every stage of production to deliver greater volumes of copper at lower economic and environmental cost.
- IEF on 'Paradox' of Mining's Role in Quest for Clean EnergySustainability
- Conflict Minerals: Navigating Ethical Sourcing ChallengesSourcing & Procurement
- How do Mining Companies Mitigate Environmental Damage?Sustainability
- Rio Tinto, BHP & Glencore 'Feeling the Pinch on Copper'Supply Chain & Operations
Featured Articles
A fleet of Huaneng Ruichi autonomous electric mining trucks have been deployed in China, supported by Huawei's Cloud Services and 5G-Advanced network
Rio Tinto completed its US$6.7bn acquisition of Arcadium Lithium, making it a key company in raw materials mining for batteries in the energy transition
Intel first began to work towards responsibly sourced conflict minerals from the Democratic Republic of Congo and adjoining countries about 12 years